Preparation method of slump-proof polycarboxylate superplasticizer
A technology of slump-preserving polycarboxylic acid and water-reducing agent, which is applied in the field of concrete admixtures, can solve the problems of poor slump-preserving effect of polycarboxylate water-reducing agent, and achieves the advantages of controllable reaction rate, stable performance and reduced production cost. Effect
- Summary
- Abstract
- Description
- Claims
- Application Information
AI Technical Summary
Problems solved by technology
Method used
Image
Examples
Embodiment 1
[0039] This embodiment provides a synthetic method of polycarboxylate water reducer, which specifically includes the following steps:
[0040] 1. Preparation of isopentenyl polyoxyethylene polyoxypropylene ether
[0041] (1) Add 125 g of isopentenol and 0.35 g of KOH alkali catalyst into the reaction kettle, and replace the air in the kettle with nitrogen.
[0042] (2) When the temperature of the kettle rises to 100°C, start feeding 2325g of ethylene oxide and 1450g of propylene oxide, keep the polymerization reaction temperature at 130°C, and the reaction pressure at 0.35Mpa. The reaction product of polyoxyethylene polyoxypropylene ether.
[0043] (3) neutralize the above-mentioned reaction product, then degas in the reactor to obtain m=30, n=20, isopentenyl polyoxyethylene polyoxypropylene ether with an average molecular weight of 2553.16.
[0044] 2. Preparation of polycarboxylate water reducer
[0045] (1) In a four-necked flask, add 250 g of isopentenyl polyoxyethylene...
Embodiment 2
[0050] This embodiment provides a synthetic method of polycarboxylate water reducer, which specifically includes the following steps:
[0051] 1. Preparation of isobutylene-based polyoxyethylene polyoxypropylene ether
[0052] (1) Add 100 g of isobutenol and 0.25 g of KOH base catalyst into a 2L reaction kettle, and replace the air in the kettle with nitrogen.
[0053] (2) When the temperature of the kettle rises to 100-110°C, start to feed 1620g of ethylene oxide and 935g of propylene oxide, keep the polymerization reaction temperature at 100°C, and the reaction pressure at 0.25Mpa. After 3 hours of aging, the isobutylene-containing The reaction product of polyoxyethylene polyoxypropylene ether.
[0054] (3) neutralize the above-mentioned reaction product, then degas in the reactor to obtain m=42, n=5, isobutylene-based polyoxyethylene polyoxypropylene ether with an average molecular weight of 2210.58.
[0055] 2. Preparation of polycarboxylate water reducer
[0056] (1) I...
Embodiment 3
[0061] This embodiment provides a synthetic method of polycarboxylate water reducer, which specifically includes the following steps:
[0062] 1. Preparation of isopentenyl polyoxyethylene polyoxypropylene ether
[0063] (1) Add 85 g of isopentenol and 0.35 g of KOH as an alkali catalyst into the reaction kettle, and replace the air in the kettle with nitrogen.
[0064] (2) When the temperature of the kettle rises to 100-110°C, start to feed 2440g of ethylene oxide and 800g of propylene oxide, keep the polymerization reaction temperature at 125°C, and the reaction pressure at 0.35Mpa. The reaction product of pentenyl polyoxyethylene polyoxypropylene ether.
[0065] (3) neutralize the above-mentioned reaction product, and then degas in the reactor to obtain m=48, n=17, isopentenyl polyoxyethylene polyoxypropylene ether with an average molecular weight of 3171.8.
[0066] 2. Preparation of polycarboxylate water reducer
[0067] (1) In a four-necked flask, add 270 g of isopent...
PUM
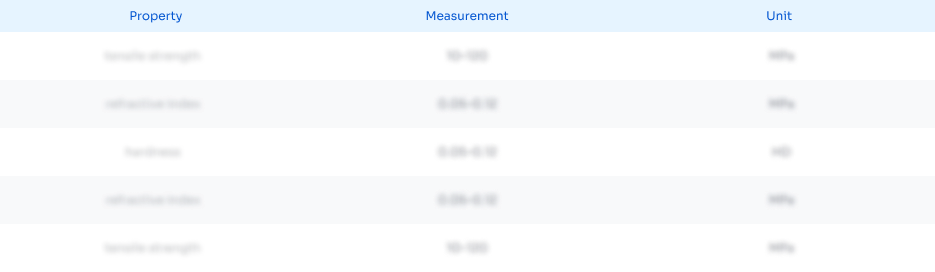
Abstract
Description
Claims
Application Information

- R&D
- Intellectual Property
- Life Sciences
- Materials
- Tech Scout
- Unparalleled Data Quality
- Higher Quality Content
- 60% Fewer Hallucinations
Browse by: Latest US Patents, China's latest patents, Technical Efficacy Thesaurus, Application Domain, Technology Topic, Popular Technical Reports.
© 2025 PatSnap. All rights reserved.Legal|Privacy policy|Modern Slavery Act Transparency Statement|Sitemap|About US| Contact US: help@patsnap.com