Preparation method and application of anti-blue-ray film
An anti-blue light and microsphere technology, which is applied in optics, optical components, instruments, etc., can solve the problems of high technical threshold and few involvements
- Summary
- Abstract
- Description
- Claims
- Application Information
AI Technical Summary
Problems solved by technology
Method used
Image
Examples
Embodiment 1
[0029] Step (1) preparation of blue light reflective film
[0030] Using a 1L oil-bath stirred tank, protected by high-purity nitrogen, pre-mix 500g deionized water, 100g styrene, 10g methyl methacrylate, 10g acrylic acid, 2.5g ammonium bicarbonate, 2g sodium dodecylbenzenesulfonate, Stir at 70°C for about 30 minutes, then add a mixed solution of 3g ammonium persulfate and deionized water, and react at 75°C for two hours; then slowly add 5g ethyl acrylate, 5g propyl methacrylate, 0.2g A mixture of sodium dodecylbenzenesulfonate, 0.2g potassium hydroxide, and 100g deionized water to form a buffer layer; finally add a mixture of 100g ethyl acrylate and 0.2g sodium dodecylbenzenesulfonate in 120 minutes , 100g of deionized water mixture, and then react at 90°C for 60 minutes to allow the organic monomers to fully react. The composite microspheres were obtained by breaking the emulsion with methanol and drying.
[0031] After the composite microspheres are subjected to hot press...
Embodiment 2
[0033] Step (1) preparation of visible light reflective film
[0034] Use a 1L oil-bath stirred tank, protected by high-purity nitrogen, pre-mix 500g deionized water, 100g methyl methacrylate, 10g acrylic acid, 2.5g ammonium bicarbonate, 1g sodium dodecylbenzenesulfonate, stir at 70°C About 30 minutes, then add a mixed solution of 3g ammonium persulfate and deionized water, react at 75°C for two hours; then slowly add 5g ethyl acrylate, 5g propyl methacrylate, 0.2g dodecyl over 60 minutes A mixture of sodium benzenesulfonate, 0.2g potassium hydroxide, and 100g deionized water to form a buffer layer; finally, add a mixture of 100g ethyl acrylate, 0.2g sodium dodecylbenzenesulfonate, and 100g deionized water for 120 minutes. Water mixture, then react at 90°C for 60 minutes to allow the organic monomers to fully react. The composite microspheres were obtained by breaking the emulsion with methanol and drying.
[0035] After the composite microspheres are subjected to 130°C and ...
Embodiment 3
[0037] Preparation of anti-blue light film
[0038] Use a 1L oil-bath stirred tank, protected by high-purity nitrogen, pre-mix 500g deionized water, 100g styrene, 10g methyl methacrylate, 10g acrylic acid, 2.5g ammonium bicarbonate, 0.1g sodium dodecylbenzenesulfonate , stirred at 70°C for about 30 minutes, then added a mixed solution of 3g ammonium persulfate and deionized water, and reacted at 75°C for two hours; then slowly added 5g ethyl acrylate, 5g propyl methacrylate, 0.2 The mixed solution of sodium dodecylbenzene sulfonate, 0.2g potassium hydroxide, and 100g deionized water form a buffer layer; finally add a mixture of 100g ethyl acrylate and 0.2g sodium dodecylbenzenesulfonate in 120 minutes Liquid, 100g deionized water mixed solution, and then reacted at 90°C for 60 minutes to allow the organic monomers to fully react. The composite microspheres were obtained by breaking the emulsion with methanol and drying.
[0039] The composite microspheres can be hot-pressed ...
PUM
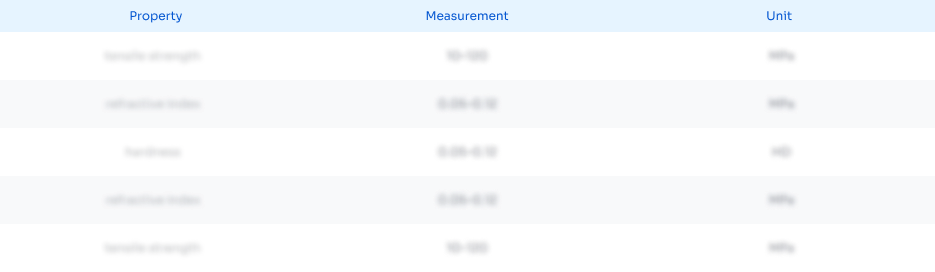
Abstract
Description
Claims
Application Information

- R&D
- Intellectual Property
- Life Sciences
- Materials
- Tech Scout
- Unparalleled Data Quality
- Higher Quality Content
- 60% Fewer Hallucinations
Browse by: Latest US Patents, China's latest patents, Technical Efficacy Thesaurus, Application Domain, Technology Topic, Popular Technical Reports.
© 2025 PatSnap. All rights reserved.Legal|Privacy policy|Modern Slavery Act Transparency Statement|Sitemap|About US| Contact US: help@patsnap.com