High-flame-retardance polyvinyl chloride resin and preparation method thereof
A polyvinyl chloride resin and a high flame retardant technology are applied in the field of high flame retardant polyvinyl chloride resin and its preparation, and can solve the problems of insufficient flame retardant performance of the polyvinyl chloride resin and the like
- Summary
- Abstract
- Description
- Claims
- Application Information
AI Technical Summary
Problems solved by technology
Method used
Image
Examples
preparation example Construction
[0020] The preparation method of described high flame-retardant polyvinyl chloride resin comprises the following steps:
[0021] S1. Mix polyvinyl chloride resin, epoxy resin, phenolic resin, polyphenylene ether, EVA resin, and phthalic anhydride polyester polyol evenly, heat up to 70-80°C, keep warm for 20-30min, then add talcum powder and stearic acid Mix zinc, cerium oxide, antimony trioxide, wood fiber powder, glass fiber, aluminum tripolyphosphate, zinc borate, chlorinated paraffin and epichlorohydrin, continue to heat up to 70-80°C, keep warm for 30-50min, then Stir at 350-450r / min for 10-20min, cool to room temperature to obtain the base material;
[0022]S2. Mix maleic anhydride, magnesium hydroxide, silane coupling agent KH-560 and flame retardant modification additive evenly, heat up to 80-90°C, keep warm for 20-40min, and then stir at 1500-2500r / min for 5 -15min, cooled to room temperature to obtain modified material;
[0023] S3. Heat the base material to 60-80°C...
Embodiment 1
[0026] A high flame-retardant polyvinyl chloride resin, in parts by weight, comprising the following raw materials: 45 parts of polyvinyl chloride resin, 25 parts of epoxy resin, 10 parts of phenolic resin, 6 parts of polyphenylene ether, 3 parts of EVA resin, 4.5 parts of phthalic anhydride polyester polyol, 3.5 parts of ethylene-vinyl acetate copolymer, 3 parts of trioctyl trimellitate, 4.5 parts of styrene, 3 parts of dicumyl peroxide, 3 parts of tricresyl phosphate, polyethylene 4 parts of lactone, 6 parts of talcum powder, 4.5 parts of zinc stearate, 3.5 parts of cerium oxide, 3 parts of antimony trioxide, 4.5 parts of wood fiber powder, 3.5 parts of glass fiber, 3 parts of aluminum tripolyphosphate, 4.5 parts of zinc borate 6 parts of chlorinated paraffin, 4.5 parts of epichlorohydrin, 8 parts of maleic anhydride, 10 parts of magnesium hydroxide, 3 parts of silane coupling agent KH-560, and 15 parts of flame retardant modification additive.
[0027] The flame retardant m...
Embodiment 2
[0033] A high flame-retardant polyvinyl chloride resin, in parts by weight, comprising the following raw materials: 40 parts of polyvinyl chloride resin, 30 parts of epoxy resin, 5 parts of phenolic resin, 8 parts of polyphenylene ether, 1 part of EVA resin, 6 parts of phthalic anhydride polyester polyol, 2 parts of ethylene-vinyl acetate copolymer, 5 parts of trioctyl trimellitate, 3 parts of styrene, 5 parts of dicumyl peroxide, 1 part of tricresyl phosphate, polyethylene 6 parts of lactone, 4 parts of talcum powder, 6 parts of zinc stearate, 2 parts of cerium oxide, 5 parts of antimony trioxide, 3 parts of wood fiber powder, 5 parts of glass fiber, 1 part of aluminum tripolyphosphate, 6 parts of zinc borate 4 parts, 4 parts of chlorinated paraffin, 6 parts of epichlorohydrin, 6 parts of maleic anhydride, 12 parts of magnesium hydroxide, 2 parts of silane coupling agent KH-560, 20 parts of flame retardant modification additive.
[0034] The flame retardant modification addit...
PUM
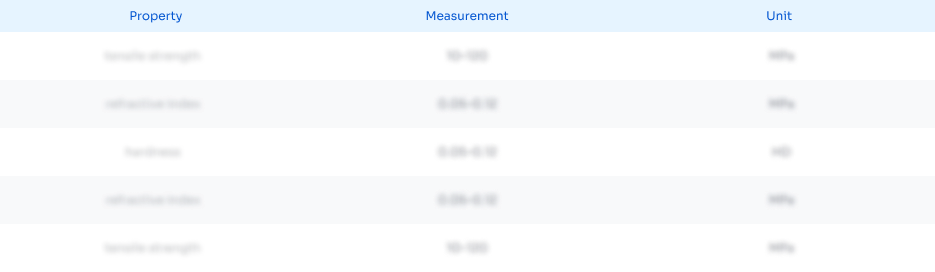
Abstract
Description
Claims
Application Information

- Generate Ideas
- Intellectual Property
- Life Sciences
- Materials
- Tech Scout
- Unparalleled Data Quality
- Higher Quality Content
- 60% Fewer Hallucinations
Browse by: Latest US Patents, China's latest patents, Technical Efficacy Thesaurus, Application Domain, Technology Topic, Popular Technical Reports.
© 2025 PatSnap. All rights reserved.Legal|Privacy policy|Modern Slavery Act Transparency Statement|Sitemap|About US| Contact US: help@patsnap.com