Plastic part polishing and burnishing method
A component and plastic technology, applied in the field of automotive plastic parts processing, can solve the problems of high grinding cost and poor uniformity, achieve high processing efficiency and avoid deformation
- Summary
- Abstract
- Description
- Claims
- Application Information
AI Technical Summary
Problems solved by technology
Method used
Image
Examples
Embodiment Construction
[0022] Further detailed explanation through specific implementation mode below:
[0023] The reference signs in the drawings of the description include: propulsion cylinder 1, piston plate 2, piston rod 3, hollow shaft 4, spline sleeve 5, adsorption port 6, electrostatic brush 7, support lever 8, grinding and polishing set 9, gear 10. Motor 11, guide sleeve 12, polishing block 13, tension spring 14, clamping cylinder 15, clamping block 16, adsorption channel 17.
[0024] The embodiment of plastic parts grinding and polishing method is basically as attached figure 1 And attached figure 2 Shown:
[0025] Include the following steps:
[0026] Step 1, preparation, requires the use of plastic parts grinding and polishing equipment, which includes a frame and a parts clamping device and a grinding and polishing device located on the frame; the grinding and polishing device includes a working push cylinder horizontally arranged on the frame 1. The piston plate 2 of the propulsio...
PUM
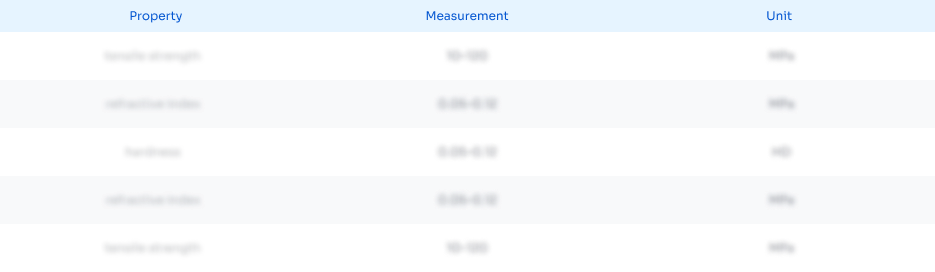
Abstract
Description
Claims
Application Information

- R&D
- Intellectual Property
- Life Sciences
- Materials
- Tech Scout
- Unparalleled Data Quality
- Higher Quality Content
- 60% Fewer Hallucinations
Browse by: Latest US Patents, China's latest patents, Technical Efficacy Thesaurus, Application Domain, Technology Topic, Popular Technical Reports.
© 2025 PatSnap. All rights reserved.Legal|Privacy policy|Modern Slavery Act Transparency Statement|Sitemap|About US| Contact US: help@patsnap.com