A Full-Order Observer Velocity Sensorless Control System Based on Error Weighting
A speed sensorless, full-order observer technology, used in control systems, vector control systems, control generators, etc., to solve problems such as low-speed instability
- Summary
- Abstract
- Description
- Claims
- Application Information
AI Technical Summary
Problems solved by technology
Method used
Image
Examples
Embodiment Construction
[0070] The embodiments of the present invention are described in detail below. This embodiment is implemented on the premise of the technical solution of the present invention, and detailed implementation methods and specific operating procedures are provided, but the protection scope of the present invention is not limited to the following implementation example.
[0071] see Figure 1 to Figure 3 , a full-order observer-based speed sensorless control strategy based on error weighting of the present invention is applied in a full-order observer-based speed sensorless control system based on error weighting, and the full-order observer speed sensorless control system based on error weighting includes SVPWM , inverter, IM, two Clark modules, two Park modules, one anti-Park module, full-order observer, first comparator, first regulator, second comparator, second regulator, third comparator device, a third regulator, a slip calculation module, a first adder, and an integrator. ...
PUM
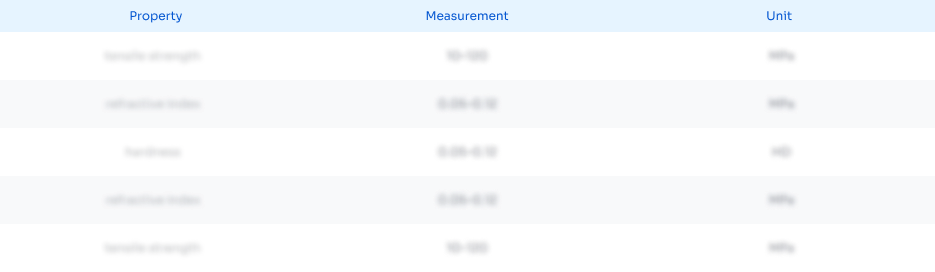
Abstract
Description
Claims
Application Information

- R&D
- Intellectual Property
- Life Sciences
- Materials
- Tech Scout
- Unparalleled Data Quality
- Higher Quality Content
- 60% Fewer Hallucinations
Browse by: Latest US Patents, China's latest patents, Technical Efficacy Thesaurus, Application Domain, Technology Topic, Popular Technical Reports.
© 2025 PatSnap. All rights reserved.Legal|Privacy policy|Modern Slavery Act Transparency Statement|Sitemap|About US| Contact US: help@patsnap.com