Torsion beam welding assembly structure
An assembly structure, torsion beam technology, applied in interconnection systems, suspensions, transportation and packaging, etc., can solve the problems of inability to increase torsion bars, difficult to ensure welding quality, and difficult to roll stiffness, etc., to achieve robot welding, Easy robot welding, the effect of reducing the number of welds
- Summary
- Abstract
- Description
- Claims
- Application Information
AI Technical Summary
Problems solved by technology
Method used
Image
Examples
Embodiment 1
[0023] Such as Figure 2-5 As shown, the torsion beam welding assembly structure of this embodiment includes two facades 101 of a channel-shaped upper plate 100 with a "C"-shaped cross-section and two groove-shaped lower plates 200 with a "C"-shaped cross-section. Facade 201 is a sheet metal structure formed by fastening and welding, such as Figure 4 As shown, the overlap between the upper and lower panels is generally controlled at about 5mm. The sheet metal structure is divided into a beam section 110 located in the middle, a left end section 140 located at the left end, a right end section 150 located at the right end, a left transition section 120 located between the beam section 110 and the left end section 140, and a section located between the beam section 110 and the right end. The right transition section 130 between the parts 150; wherein the left end section 140 and the right end section 150, the left transition section 120 and the right transition section 130 are...
PUM
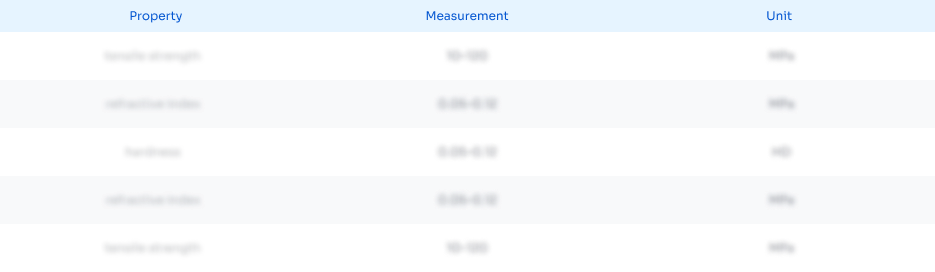
Abstract
Description
Claims
Application Information

- R&D Engineer
- R&D Manager
- IP Professional
- Industry Leading Data Capabilities
- Powerful AI technology
- Patent DNA Extraction
Browse by: Latest US Patents, China's latest patents, Technical Efficacy Thesaurus, Application Domain, Technology Topic, Popular Technical Reports.
© 2024 PatSnap. All rights reserved.Legal|Privacy policy|Modern Slavery Act Transparency Statement|Sitemap|About US| Contact US: help@patsnap.com