Method for improving molybdenum concentrate recovery rate during copper-molybdenum separation of low-grade high-argillization skarn ore
A skarn copper-molybdenum, low-grade technology, applied in the field of improving the recovery rate of copper-molybdenum separation molybdenum concentrate from skarn copper-molybdenum ore, can solve the problem of low molybdenum recovery rate
- Summary
- Abstract
- Description
- Claims
- Application Information
AI Technical Summary
Problems solved by technology
Method used
Image
Examples
Embodiment 1
[0048] Include the following steps:
[0049] (1) Pre-tailing operation of mixed concentrate:
[0050] For low-grade high-mud skarn copper-molybdenum ore, which contains low molybdenum grade and gangue minerals are easy to muddy, in order to eliminate the influence of fine-grained gangue minerals on the subsequent separation and flotation of copper and molybdenum, a tailing is removed in advance. That is, copper concentrate, throwing away part of the fine-grained gangue in advance to enrich the molybdenum grade in the copper-molybdenum mixed concentrate, and adjusting the mass percentage concentration of the mixed concentrate slurry produced by the ore-copper-molybdenum mixed concentrate to 10%; Pre-selection and tailing roughing operation: add 1450g / t of sodium silicate mixed concentrate, 3900g / t of sodium hydrosulfide mixed concentrate, 90g / t of kerosene mixed concentrate to the slurry, stir for 4 minutes, flotation time of 6 minutes, foam Enter the copper-molybdenum separat...
Embodiment 2
[0058] Include the following steps:
[0059] (1) Pre-tailing operation of mixed concentrate:
[0060]For low-grade high-mud skarn copper-molybdenum ore, which contains low molybdenum grade and gangue minerals are easy to muddy, in order to eliminate the influence of fine-grained gangue minerals on the subsequent separation and flotation of copper and molybdenum, a tailing is removed in advance. That is, copper concentrate, throwing away part of the fine-grained gangue in advance to enrich the molybdenum grade in the copper-molybdenum mixed concentrate, and adjusting the mass percentage concentration of the mixed concentrate slurry produced by the ore-copper-molybdenum mixed concentrate to 11%; Pre-selection tailing roughing operation: Add 1500g / t mixed concentrate of water glass, 4000g / t mixed concentrate of sodium hydrogen sulfide, 100g / t kerosene mixed concentrate to the pulp, stir for 5 minutes, flotation time is 7 minutes, foam Enter the copper and molybdenum separation r...
Embodiment 3
[0068] Include the following steps:
[0069] (1) Pre-tailing operation of mixed concentrate:
[0070] For low-grade high-mud skarn copper-molybdenum ore, which contains low molybdenum grade and gangue minerals are easy to muddy, in order to eliminate the influence of fine-grained gangue minerals on the subsequent separation and flotation of copper and molybdenum, a tailing is removed in advance. That is, copper concentrate, throwing away part of the fine-grained gangue in advance, so that the molybdenum grade in the copper-molybdenum mixed concentrate can be enriched, and the mass percentage concentration of the mixed concentrate slurry produced by the copper-molybdenum mixed concentrate output is adjusted to 12%; Pre-selection and tailing roughing operation: add 1550g / t of sodium silicate mixed concentrate, 4100g / t of sodium hydrosulfide mixed concentrate, 110g / t of kerosene mixed concentrate to the slurry, stir for 6 minutes, flotation time of 8 minutes, foam Enter the copp...
PUM
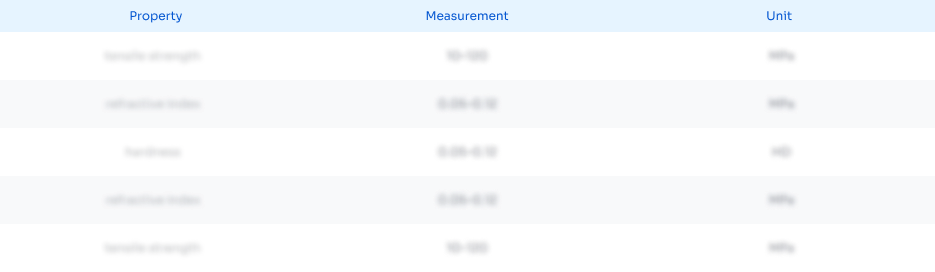
Abstract
Description
Claims
Application Information

- R&D Engineer
- R&D Manager
- IP Professional
- Industry Leading Data Capabilities
- Powerful AI technology
- Patent DNA Extraction
Browse by: Latest US Patents, China's latest patents, Technical Efficacy Thesaurus, Application Domain, Technology Topic, Popular Technical Reports.
© 2024 PatSnap. All rights reserved.Legal|Privacy policy|Modern Slavery Act Transparency Statement|Sitemap|About US| Contact US: help@patsnap.com