Method of producing water permeable brick through extrusion molding of aeolian sand
A technology of extrusion molding and permeable bricks, which is applied in applications, household appliances, clay products, etc., can solve the problems of small desert sand usage, long production cycle, and difficult operation, so as to maintain surface water circulation and solve groundwater source problems , Improve the effect of air quality
- Summary
- Abstract
- Description
- Claims
- Application Information
AI Technical Summary
Problems solved by technology
Method used
Examples
Embodiment 1
[0019] (1) Crush and sieve aeolian sand into raw material particles below 80 mesh, crush and sieve bentonite and calcite into below 80 mesh, and sieve sawdust into below 30 mesh for use; weigh raw materials according to the following weight percentage: aeolian sand 70 %, bentonite 25%, calcite 5%, sawdust 5%, stir evenly, and set aside;
[0020] (2) Add the cmc sol with a concentration of 3.5% to step (1), add 15% of the cmc sol and add 0.5% glycerin, stir well, and stale for 24 hours;
[0021] (3) Put the stale material obtained in step (2) into the extruder and extrude it;
[0022] (4) Put the green body obtained in step (3) at room temperature for 48 hours, put it in an oven at 100°C, and dry it until the water content is lower than 1%;
[0023] (5) The heating rate is 1-2°C / min from room temperature to 350°C, the heating rate is 4-5°C / min at 350°C-850, the heating rate is 1-2°C / min at 850-950°C, and the heating rate is 4-5°C / min Min firing to 1180°C, heat preservation fo...
Embodiment 2
[0025] (1) Crush and sieve aeolian sand into raw material particles below 80 mesh, crush and sieve bentonite and calcite into below 80 mesh, and sieve sawdust into below 30 mesh for use; weigh raw materials according to the following weight percentage: aeolian sand 65 %, bentonite 25%, calcite 10%, sawdust 4%, stir evenly, and set aside;
[0026] (2) Add the cmc sol with a concentration of 4% to step (1), add 18% of the cmc sol and add 0.8% glycerin, stir well, and stale for 24 hours;
[0027] (3) Add the extruding material obtained in step (2) into an extruding machine, and extrude;
[0028] (4) Put the green body obtained in step (3) at room temperature for 48 hours, put it in an oven at 110°C, and dry it until the moisture content is lower than 1%;
[0029] (5) The heating rate is 1-2°C / min from room temperature to 350°C, 4-5°C / min at 350°C-850, 1-2°C / min at 850-950°C, and 4-5°C / min at 850-950°C. Min firing to 1180°C, heat preservation for 20 minutes, and cooling to room ...
Embodiment 3
[0031] (1) Crush and sieve aeolian sand into raw material particles below 80 mesh, crush and sieve bentonite and calcite into below 80 mesh, and sieve sawdust into below 30 mesh for use; weigh raw materials according to the following weight percentage: aeolian sand 75 %, bentonite 20%, calcite 5%, sawdust 10%, stir evenly, and set aside;
[0032] (2) Add the cmc solution with a concentration of 3% to step (1), add 12% of the cmc sol and add 0.8% glycerin, stir evenly, and stale;
[0033] (3) Add the extruding material obtained in step (2) into an extruding machine, and extrude;
[0034] (4) Put the green body obtained in step (3) at room temperature for 48 hours, put it in an oven at 80°C, and dry it until the water content is lower than 1%;
[0035] (5) From room temperature to 350°C, the heating rate is 1-2°C / min, at 350°C--850, the heating rate is 4-5°C / min, at 850-950°C, the heating rate is 1-2°C / min, and the heating rate is 4-5°C / min firing to 1180°C, heat preservation...
PUM
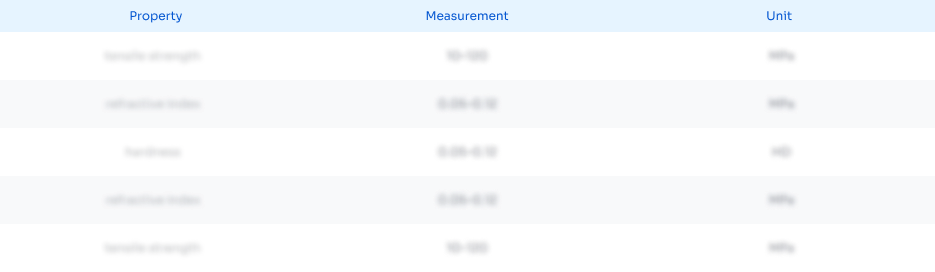
Abstract
Description
Claims
Application Information

- R&D
- Intellectual Property
- Life Sciences
- Materials
- Tech Scout
- Unparalleled Data Quality
- Higher Quality Content
- 60% Fewer Hallucinations
Browse by: Latest US Patents, China's latest patents, Technical Efficacy Thesaurus, Application Domain, Technology Topic, Popular Technical Reports.
© 2025 PatSnap. All rights reserved.Legal|Privacy policy|Modern Slavery Act Transparency Statement|Sitemap|About US| Contact US: help@patsnap.com