Stacked noise reduction self-coding motor fault diagnosis method based on vibration and current signals
A fault diagnosis and current signal technology, which is applied in the direction of motor generator testing, measuring electricity, and measuring electrical variables, etc., can solve problems such as difficult fault diagnosis of asynchronous motors and complex motor structures
- Summary
- Abstract
- Description
- Claims
- Application Information
AI Technical Summary
Problems solved by technology
Method used
Image
Examples
Embodiment Construction
[0029] Embodiments of the present invention are described in detail with reference to the accompanying drawings of the present invention.
[0030] Step 1: Collect data. Taking the asynchronous motor of the power transmission fault diagnosis comprehensive test bench as the research object, the test bench is composed of four parts: asynchronous motor, two-stage planetary gearbox, fixed shaft gearbox and magnetic powder brake. By replacing the motor to simulate 7 different fault states, as shown in Table 2, 7 different fault states are listed in the table.
[0031] Table 2 Seven states of the motor
[0032]
[0033] In order to ensure the diversity of experimental data, 10 different working conditions were simulated when collecting data, corresponding to 5 speeds (speed up and down, 3560RPM, 3580RPM, 3560RPM, 3620RPM), and 2 states (loaded and unloaded). Considering the influence of the position of the sensor, two acceleration sensors are arranged at the front end of the mot...
PUM
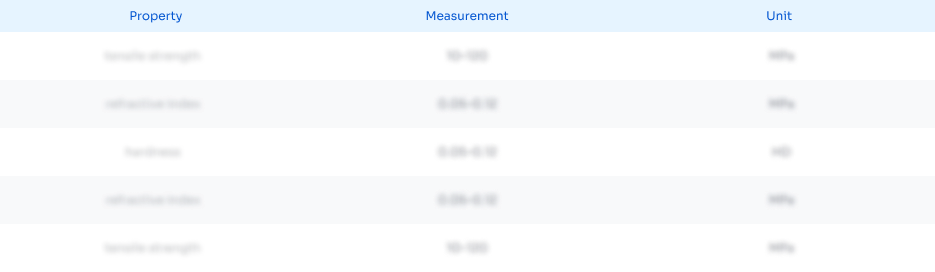
Abstract
Description
Claims
Application Information

- R&D
- Intellectual Property
- Life Sciences
- Materials
- Tech Scout
- Unparalleled Data Quality
- Higher Quality Content
- 60% Fewer Hallucinations
Browse by: Latest US Patents, China's latest patents, Technical Efficacy Thesaurus, Application Domain, Technology Topic, Popular Technical Reports.
© 2025 PatSnap. All rights reserved.Legal|Privacy policy|Modern Slavery Act Transparency Statement|Sitemap|About US| Contact US: help@patsnap.com