Preparation method of PVDF-HFP/GO composite film for increasing content of beta crystalline phase
A technology of PVDF-HFP and composite films, which is applied in the preparation of PVDF-HFP/GO composite films and PVDF-HFP composite films, can solve the problems of poor piezoelectric properties of PVDF-HFP composite films and achieve β crystal phase content Effects of increasing and improving piezoelectric properties and improving crystallinity
- Summary
- Abstract
- Description
- Claims
- Application Information
AI Technical Summary
Problems solved by technology
Method used
Image
Examples
preparation example Construction
[0033] A method for preparing a PVDF-HFP / GO composite film for increasing the content of the β crystal phase, comprising the following steps:
[0034] Step S1, polishing and cleaning the flat glass.
[0035] In order to improve the cleaning effect on the flat glass, in step S1, the cleaning step of the flat glass is: cleaning the polished flat glass with detergent to remove surface stains; then using ultra-clean water to remove residual detergent and Stains; put the cleaned flat glass into analytically pure acetone and ultrasonically clean it for 15-20 minutes; use ultra-clean water to remove acetone on the surface and then add absolute ethanol to ultrasonically clean it for 15-20 minutes to remove residual acetone; use the flat glass after ethanol Ultrasonic cleaning with ultra-clean water for 15-20 minutes, followed by drying with N2.
[0036] Step S2, mixing and stirring graphene oxide particles with a mass percentage of 0.01% to 0.1% with a solvent to prepare a graphene oxi...
Embodiment 1
[0046] A method for preparing a PVDF-HFP / GO composite film for increasing the content of the β crystal phase, comprising the following steps:
[0047] Step S1, polishing and cleaning the flat glass;
[0048] Step S2, mixing and stirring graphene oxide particles with a solvent to make a graphene oxide dispersion; then adding PVDF-HFP to the suspension to mix and stir to obtain a PVDF-HFP / Graphene oxide mixed solution; When ene particles are added to the solvent, the mass percentage of graphene oxide particles is 0.01% to 0.1%; when PVDF-HFP spherical particles are added to the graphene oxide dispersion, the mass percentage of PVDF-HFP spherical particles is 25%. ~30%;
[0049] Step S3, defoaming the PVDF-HFP / Graphene oxide mixed solution prepared in step S2 in a 0.1Mpa to 0.01Mpa vacuum box for 3 to 4 hours;
[0050] Step S4, pour the PVDF-HFP / Graphene oxide mixed solution degassed in step S3 on the flat glass after step S1 cleaning, and spread the PVDF-HFP / Graphene oxide mix...
Embodiment 2
[0053] On the basis of Embodiment 1, in order to improve the cleaning effect on the flat glass, in step S1, the cleaning step of the flat glass is: cleaning the polished flat glass with detergent to remove surface stains; then using ultra-clean water Remove residual detergent and stains on the surface; put the cleaned flat glass into acetone analytically pure and ultrasonically clean it for 15-20 minutes; use ultra-clean water to remove acetone on the surface, then add absolute ethanol and ultrasonically clean it for 15-20 minutes to remove residual acetone; The flat glass after ethanol was ultrasonically cleaned with ultra-clean water for 15-20 min, and then dried with N2.
PUM
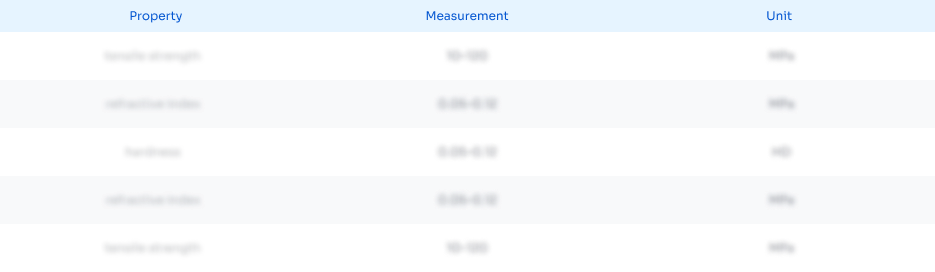
Abstract
Description
Claims
Application Information

- Generate Ideas
- Intellectual Property
- Life Sciences
- Materials
- Tech Scout
- Unparalleled Data Quality
- Higher Quality Content
- 60% Fewer Hallucinations
Browse by: Latest US Patents, China's latest patents, Technical Efficacy Thesaurus, Application Domain, Technology Topic, Popular Technical Reports.
© 2025 PatSnap. All rights reserved.Legal|Privacy policy|Modern Slavery Act Transparency Statement|Sitemap|About US| Contact US: help@patsnap.com