Vertical compression type biomass composite continuous production system and application method thereof
A composite material and production system technology, applied in the field of composite materials, can solve the problems of unbalanced mechanical properties, easy water absorption and easy winding of long fiber materials, and achieve the effect of stable quality, excellent performance and uniform composition
- Summary
- Abstract
- Description
- Claims
- Application Information
AI Technical Summary
Problems solved by technology
Method used
Image
Examples
Embodiment 1
[0044] like figure 1 As shown, the continuous production system of the direct pressure biomass composite material provided in this embodiment,
[0045] It includes a melt film forming device 1, a fiber material conveying device and a melt film forming device 2; the melt film forming device 1 includes a melt film forming machine 1 and a forming roller 12 arranged below the melt film forming machine 1 .
[0046] The fiber material conveying device includes a conveyor 2, a forming roller 2 3 and a forming roller 3 11 arranged sequentially from top to bottom; Pressing the fibrous material and the melting film one; the forming roller two 3 and the forming roller three 11 are rotated in cooperation, which is set to form a second lamination of the fibrous material and the melting film one.
[0047] The conveyor 2 of the present invention is any one of a vacuum conveyor, a screw conveyor, and a press, and a vacuum conveyor is preferred in this embodiment.
[0048] Melting film formi...
Embodiment 2
[0054] The continuous production system of the direct pressure type biomass composite material of this embodiment is the same as that of Embodiment 1, the difference is that the surface of the forming roller 2 3 is a hole structure, see for details image 3 shown.
Embodiment 3
[0056] The using method of the continuous production system using the direct pressure type biomass composite material of embodiment 1 may further comprise the steps:
[0057] S1. Put the polymer material A in the melt film forming machine 1, extrude the polymer material A on the forming roller 12 through melting and plasticizing, at the same time, add the biomass fiber material to the conveyor, and pass through the forming roller The first 12 and the second forming roller 3 are preliminarily pressed together, the first forming roller 12 and the second forming roller 3 are heated to 30~300°C, and the pressed polymer material A and the biomass fiber material 4 are transported to the second forming roller 3 and Forming roll three 11; adjust the pressure and action angle between the forming roll two and the forming roll three, so that the biomass fiber material 4 is completely closely combined with the polymer melt film A5;
[0058] S2. Put the polymer material B in the melt film ...
PUM
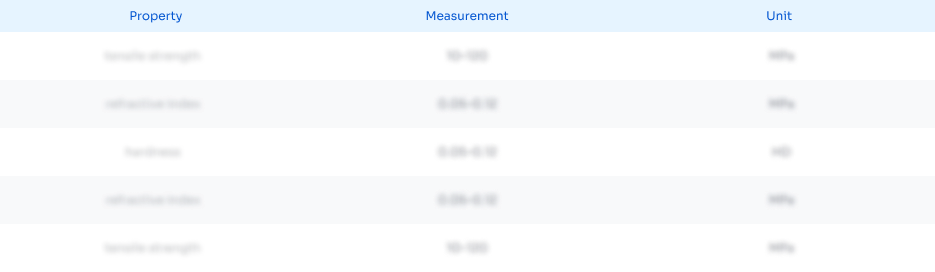
Abstract
Description
Claims
Application Information

- R&D Engineer
- R&D Manager
- IP Professional
- Industry Leading Data Capabilities
- Powerful AI technology
- Patent DNA Extraction
Browse by: Latest US Patents, China's latest patents, Technical Efficacy Thesaurus, Application Domain, Technology Topic, Popular Technical Reports.
© 2024 PatSnap. All rights reserved.Legal|Privacy policy|Modern Slavery Act Transparency Statement|Sitemap|About US| Contact US: help@patsnap.com