Method for preparation of battery grade lithium chloride from spodumene leachate
A technology of lithium chloride and leaching solution, applied in the direction of lithium halide, etc., can solve the problems of high cost, impurity removal effect, and complicated process
- Summary
- Abstract
- Description
- Claims
- Application Information
AI Technical Summary
Problems solved by technology
Method used
Image
Examples
Embodiment 1
[0053] A, adding 2.5g mass percentage concentration to 32% sodium hydroxide solution to adjust the pH value of the solution to 11 in 1L of lithium sulfate spodumene leaching liquid solution with a mass percentage concentration of 10%, warming up to 90°C, after reacting for 0.5h, According to the calculation of the Ca content in the lithium sulfate crude liquid, add 1 g of soda ash solid in an equimolar amount to the Ca content, keep the reaction temperature at 90° C. and react for 0.5 h. After the reaction is completed, filter and separate to remove the iron-magnesium slag to obtain the primary refined lithium sulfate solution 1;
[0054] B, the primary lithium sulfate refining solution 1 obtained by step A is removed Ca ion through chelating resin to obtain secondary lithium sulfate refining solution;
[0055] C, in the secondary lithium sulfate refining solution obtained in step B, according to the molar weight of sulfate radical in the secondary lithium sulfate refining solu...
Embodiment 2
[0061] A. Add 3g of 32% sodium hydroxide solution in 1L of lithium sulfate spodumene leaching solution with a mass percentage concentration of 10%, adjust the pH value to 13, heat up to 95°C, react for 1h, and then react according to lithium sulfate Calculate the Ca content in the crude liquid by adding 1 g of soda ash solid in an equimolar amount to the Ca content, and keep it at 95°C for 1 hour. After the reaction, filter and separate to remove the iron-magnesium slag to obtain a primary refined lithium sulfate solution;
[0062] The primary lithium sulfate refining solution that B, A step obtains obtains secondary lithium sulfate refining solution through chelating resin decalcification;
[0063]C, in the secondary lithium sulfate refining liquid that B step obtains, add barium chloride solid 336g according to the sulfate root molar weight in the secondary lithium sulfate refining liquid in the secondary lithium sulfate refining liquid by barium chloride: sulfate root molar ...
Embodiment 3
[0069] A, adding 2.5g mass percentage concentration to 32% sodium hydroxide solution to adjust the pH value of the solution to 11 in 1L of lithium sulfate spodumene leaching liquid solution with a mass percentage concentration of 10%, warming up to 90°C, after reacting for 0.5h, According to the calculation of the Ca content in the lithium sulfate crude liquid, add 1 g of soda ash solid in an equimolar amount to the Ca content, keep the reaction temperature at 90° C. and react for 0.5 h. After the reaction is completed, filter and separate to remove the iron-magnesium slag to obtain the primary refined lithium sulfate solution 1;
[0070] B, the primary lithium sulfate refining solution that step A obtains obtains secondary lithium sulfate refining solution through chelating resin deionization;
[0071] C, in the secondary lithium sulfate refining solution that step B obtains, according to the molar weight of sulfate in the secondary lithium sulfate refining solution, add bariu...
PUM
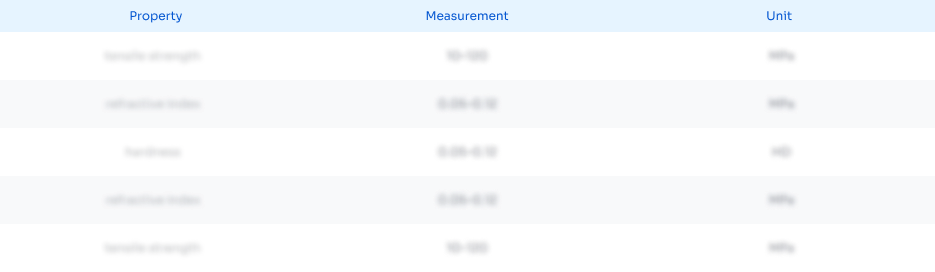
Abstract
Description
Claims
Application Information

- R&D
- Intellectual Property
- Life Sciences
- Materials
- Tech Scout
- Unparalleled Data Quality
- Higher Quality Content
- 60% Fewer Hallucinations
Browse by: Latest US Patents, China's latest patents, Technical Efficacy Thesaurus, Application Domain, Technology Topic, Popular Technical Reports.
© 2025 PatSnap. All rights reserved.Legal|Privacy policy|Modern Slavery Act Transparency Statement|Sitemap|About US| Contact US: help@patsnap.com