A method for extracting lignin from papermaking black liquor by magnetic emulsion liquid membrane separation
A technology of lignin and emulsion, which is applied in the field of papermaking, can solve the problems affecting the repeated use of oil phase and the quality of oil phase, and achieve the effects of avoiding excessive use and resource consumption, high recycling rate, avoiding use and resource consumption
- Summary
- Abstract
- Description
- Claims
- Application Information
AI Technical Summary
Problems solved by technology
Method used
Examples
Embodiment 1
[0064] FeCl 3 .6H 2 O and FeSO 4 .7H 2 O was dispersed in 100mL deionized water according to the molar ratio of 2:1 and transferred to a 250ml three-necked flask and stirred to become brick red (it took half an hour); then heated in a water bath to 50°C, and the pH value was adjusted to 11.0-12.0 with NaOH; Temperature to 65°C, stir until it turns black (2 hours); add 2 times the mass of oleic acid, continue to stir and raise the temperature to 65°C, adjust the pH to 6.0-7.0, react for 2 hours and remove the black precipitate with deionized water and acetone Repeated magnetic decantation cleaning to remove excess oleic acid; dried the obtained particles in a vacuum oven at 60°C overnight to obtain oleic acid-modified nano-Fe 3 o 4 Particles (i.e. nano-Fe 3 o 4 modified particles).
[0065] 0.5 phr nano-Fe 3 o 4 The modified particles and 3 parts of carrier TBP were dispersed in 100 parts of rapeseed oil, and ultrasonically dispersed for 15 minutes to make them uniform...
Embodiment 2
[0070] FeCl 3 .6H 2 O and FeSO 4 .7H 2 O was dispersed in 100mL of deionized water at a molar ratio of 2:1 and transferred to a 250ml three-necked flask and stirred until it turned brick red (it took half an hour); heated to 50°C in a water bath, 3 .H 2 O to adjust the pH to 11.0-12.0. Raise the temperature to 65°C and stir until it turns black (2 hours); add 5 times oleic acid, continue to stir and raise the temperature to 65°C, adjust the pH value to 6.0-7.0, react for 2 hours and remove the black precipitate with deionized water and acetone Repeated magnetic decantation cleaning to remove excess oleic acid; dried the obtained particles in a vacuum oven at 60°C overnight to obtain oleic acid-modified nano-Fe 3 o 4 Particles (i.e., nano-Fe 3 o 4 modified particles).
[0071] 1.0 parts of nano-Fe 3 o 4 The modified particles and 3 parts of carrier Cyanex 923 were dispersed in 100 parts of the oil phase, and ultrasonically dispersed for 30 minutes to make the dispers...
Embodiment 3
[0076] FeCl 3 .6H 2 O and FeSO 4 .7H 2 O was dispersed in 100mL deionized water at a molar ratio of 2:1 and transferred to a 250ml three-necked flask and stirred until it turned brick red (it took half an hour); then heated to 50°C in a water bath, and 3 .H 2 O to adjust the pH value to 11.0-12.0; raise the temperature to 65°C, stir until it turns black (2 hours); then add 3 times oleic acid, continue to stir and raise the temperature to 65°C, adjust the pH value to 6.0-7.0, and react After 2 hours, the black precipitate was repeatedly washed by magnetic decantation with deionized water and acetone to remove excess oleic acid, and the obtained particles were dried overnight in a vacuum oven at 60°C to obtain oleic acid-modified nano-Fe 3 o 4 Particles (i.e., nano-Fe 3 o 4 modified particles).
[0077] 2.0 parts nano-Fe 3 o 4 The modified particles and 3 parts of carrier Cyanex 923 were dispersed in 100 parts of oil phase, ultrasonically dispersed for 30 minutes to di...
PUM
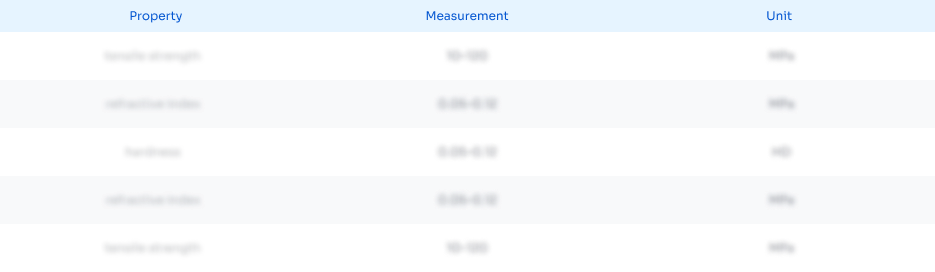
Abstract
Description
Claims
Application Information

- R&D
- Intellectual Property
- Life Sciences
- Materials
- Tech Scout
- Unparalleled Data Quality
- Higher Quality Content
- 60% Fewer Hallucinations
Browse by: Latest US Patents, China's latest patents, Technical Efficacy Thesaurus, Application Domain, Technology Topic, Popular Technical Reports.
© 2025 PatSnap. All rights reserved.Legal|Privacy policy|Modern Slavery Act Transparency Statement|Sitemap|About US| Contact US: help@patsnap.com