Anti-felting finishing method of wool fabric
A wool fabric, anti-felting technology, applied in the field of textile processing, can solve the problems of limited promotion, increased cost, complicated process, etc., and achieve the effects of improved breaking strength and softness, good dimensional stability, and simple process flow
- Summary
- Abstract
- Description
- Claims
- Application Information
AI Technical Summary
Problems solved by technology
Method used
Examples
Embodiment 1
[0011] A kind of anti-felting finishing method of wool fabric, comprises the following steps:
[0012] Step 1. Keep the water content of the woolen fabric at 30% by spraying, put it into hot water at 90-100°C for pre-cooking, and then roll it at 130-140°C, wherein the finishing solution consists of the following parts by weight: The composition of the number: 13 parts of methacryloxypropyltrimethoxysilane, 10 parts of tea saponin, 3 parts of titanium isopropoxide, 3 parts of sophorolipid, 4 parts of o-hydroxybenzoic acid ester, seven 3 parts of sodium sulfite water, 12 parts of guar hydroxypropyltrimethylammonium chloride, 10 parts of linolenic acid, 1 part of sodium polyaspartate;
[0013] Step 2. Put the wool fabric coated with the finishing solution into a drying room at 160-170°C and bake at a speed of 30-35m / min;
[0014] Step 3. Oscillating drying is used for secondary baking, the baking temperature is 130-140°C, and the speed is 25-30m / min.
Embodiment 2
[0016] A kind of anti-felting finishing method of wool fabric, comprises the following steps:
[0017] Step 1. Keep the water content of the woolen fabric at 30% by spraying, put it into hot water at 90-100°C for pre-cooking, and then roll it at 130-140°C, wherein the finishing solution consists of the following parts by weight: The composition of the number of components: 18 parts of methacryloxypropyl trimethoxysilane, 14 parts of tea saponin, 6 parts of titanium isopropoxide, 6 parts of sophorolipid, 9 parts of o-hydroxybenzoate, seven 6 parts of sodium sulfite water, 14 parts of guar gum hydroxypropyltrimethylammonium chloride, 20 parts of linolenic acid, 5 parts of sodium polyaspartate;
[0018] Step 2. Put the wool fabric coated with the finishing solution into a drying room at 160-170°C and bake at a speed of 30-35m / min;
[0019] Step 3. Oscillating drying is used for secondary baking, the baking temperature is 130-140°C, and the speed is 25-30m / min.
Embodiment 3
[0021] A kind of anti-felting finishing method of wool fabric, comprises the following steps:
[0022] Step 1. Keep the water content of the woolen fabric at 30% by spraying, put it into hot water at 90-100°C for pre-cooking, and then roll it at 130-140°C, wherein the finishing solution consists of the following parts by weight: The composition of the number of components: 15.5 parts of methacryloxypropyltrimethoxysilane, 12 parts of tea saponin, 4.5 parts of titanium isopropoxide, 4.5 parts of sophorolipids, 6.5 parts of o-hydroxybenzoate, seven 4.5 parts of sodium sulfite water, 13 parts of guar gum hydroxypropyltrimethylammonium chloride, 15 parts of linolenic acid, 3 parts of sodium polyaspartate;
[0023] Step 2. Put the wool fabric coated with the finishing solution into a drying room at 160-170°C and bake at a speed of 30-35m / min;
[0024] Step 3. Oscillating drying is used for secondary baking, the baking temperature is 130-140°C, and the speed is 25-30m / min.
[0025...
PUM
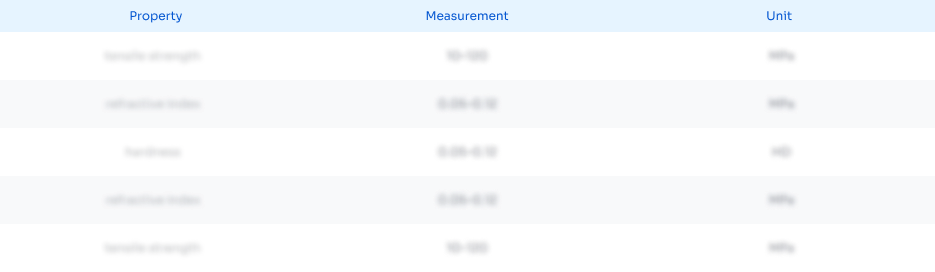
Abstract
Description
Claims
Application Information

- R&D
- Intellectual Property
- Life Sciences
- Materials
- Tech Scout
- Unparalleled Data Quality
- Higher Quality Content
- 60% Fewer Hallucinations
Browse by: Latest US Patents, China's latest patents, Technical Efficacy Thesaurus, Application Domain, Technology Topic, Popular Technical Reports.
© 2025 PatSnap. All rights reserved.Legal|Privacy policy|Modern Slavery Act Transparency Statement|Sitemap|About US| Contact US: help@patsnap.com