Manufacturing method of compressor crankshaft
A technology of a compressor crankshaft and a manufacturing method, applied in the field of powder metallurgy, can solve the problems of easily polluted environment, low production efficiency, large energy consumption of casting process, etc.
- Summary
- Abstract
- Description
- Claims
- Application Information
AI Technical Summary
Problems solved by technology
Method used
Image
Examples
Embodiment 1
[0016] A method for manufacturing a compressor crankshaft, the preparation method is as follows:
[0017] (1) Mix iron powder, aluminum powder, copper powder, tin powder, niobium powder, vanadium powder, manganese, chromium, and nano-titanium dioxide powder at 80-100°C for 60-80 minutes, then heat to 180-200°C , then add boron, silicon nitride, cuprous thiocyanate, antimony trisulfide powder, and carbon powder, cool to 100-120°C, put into the mold, press into a billet, and then naturally cool to room temperature, and the pressing pressure is 100-120°C. 200MPa;
[0018] (2) Place the green compact obtained in step (1) in a closed sintering furnace for sintering. The heating process of sintering is that the heating rate between room temperature and 900 °C is 14 °C / min, and the temperature is kept at 900 °C for 30 minutes. The heating rate from ℃ to 1320℃ is 9℃ / min, and the temperature is kept at 1320℃ for 60min. The pressure in the closed sintering furnace is not more than 0.02...
Embodiment 2
[0021] Embodiment 2: a kind of manufacturing method of compressor crankshaft, preparation method is as follows:
[0022] (1) Mix iron powder, aluminum powder, copper powder, tin powder, niobium powder, vanadium powder, manganese, chromium, and nano-titanium dioxide powder at 80-100°C for 60-80 minutes, then heat to 180-200°C , then add boron, silicon nitride, cuprous thiocyanate, antimony trisulfide powder, and carbon powder, cool to 100-120°C, put into the mold, press into a billet, and then naturally cool to room temperature, and the pressing pressure is 100-120°C. 200MPa;
[0023] (2) Place the green compact obtained in step (1) in a closed sintering furnace for sintering. The heating process of sintering is that the heating rate between room temperature and 900 °C is 14 °C / min, and the temperature is kept at 900 °C for 30 minutes. The heating rate from ℃ to 1320℃ is 9℃ / min, and the temperature is kept at 1320℃ for 60min. The pressure in the closed sintering furnace is not...
Embodiment 3
[0028] A method for manufacturing a compressor crankshaft, the preparation method is as follows:
[0029] (1) Mix iron powder, aluminum powder, copper powder, tin powder, niobium powder, vanadium powder, manganese, chromium, and nano-titanium dioxide powder at 80-100°C for 60-80 minutes, then heat to 180-200°C , then add boron, silicon nitride, cuprous thiocyanate, antimony trisulfide powder, and carbon powder, cool to 100-120°C, put into the mold, press into a billet, and then naturally cool to room temperature, and the pressing pressure is 100-120°C. 200MPa;
[0030] (2) Place the green compact obtained in step (1) in a closed sintering furnace for sintering. The heating process of sintering is that the heating rate between room temperature and 900 °C is 14 °C / min, and the temperature is kept at 900 °C for 30 minutes. The heating rate from ℃ to 1320℃ is 9℃ / min, and the temperature is kept at 1320℃ for 60min. The pressure in the closed sintering furnace is not more than 0.02...
PUM
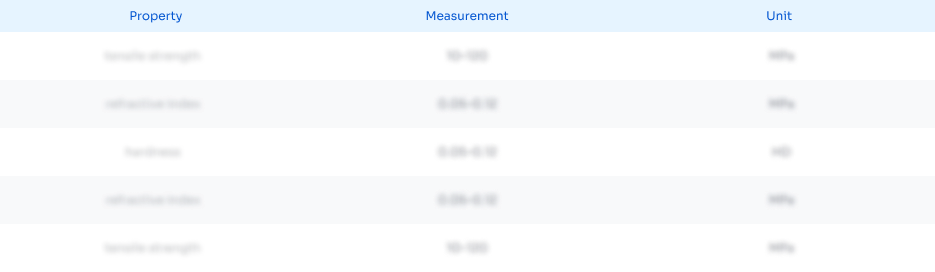
Abstract
Description
Claims
Application Information

- R&D Engineer
- R&D Manager
- IP Professional
- Industry Leading Data Capabilities
- Powerful AI technology
- Patent DNA Extraction
Browse by: Latest US Patents, China's latest patents, Technical Efficacy Thesaurus, Application Domain, Technology Topic, Popular Technical Reports.
© 2024 PatSnap. All rights reserved.Legal|Privacy policy|Modern Slavery Act Transparency Statement|Sitemap|About US| Contact US: help@patsnap.com