Process for producing deiphenyl carbonate by using non-solvent method
A technology of diphenyl carbonate and non-solvent method, applied in the field of production technology of diphenyl carbonate, can solve the problems of unstable appearance and color, complicated synthesis procedures, low product quality, etc., and avoids sodium chloride mother liquor and waste water. , the effect of reducing production costs and simplifying operations
- Summary
- Abstract
- Description
- Claims
- Application Information
AI Technical Summary
Problems solved by technology
Method used
Examples
Embodiment 1
[0035] Put 282g of phenol into a 500ml reaction bottle, heat up and melt, and when it reaches 115°C, add an appropriate amount of catalyst DMF according to 1% of the weight of phenol. Under stirring conditions, control the flow rate and slowly feed phosgene to ensure that the phosgene reaction is complete; after 12 hours of photochemistry,
[0036] Sampling analysis: 2.1% phenol, 0.9% phenyl chloroformate, 96.3% diphenyl carbonate, the reaction is over; the actual molar ratio of phenol to phosgene is 1:0.8. Raise the temperature to 150° C. and keep it warm for 3 hours, and the measured phenyl chloroformate content is <0.1% as the end point. Using oil bath heating distillation process, the oil temperature is 180°C, the internal temperature is 150°C, and the vacuum degree is 0.085Mpa, and the phenol is distilled and separated; the oil temperature is 220°C, the internal temperature is 190°C, and the vacuum degree is 0.096Mpa, and the product is obtained by distillation.
Embodiment 2
[0038] Put 282g of phenol into a 500ml reaction bottle, heat up and melt, and when it reaches 115°C, add an appropriate amount of catalyst N,N-dimethylaniline according to 1.1% of the weight of phenol. Under stirring conditions, control the flow rate and slowly feed phosgene to ensure that the phosgene reaction is complete; the photochemical time is 13 hours, sampling analysis: 3.7% phenol, 3.3% phenyl chloroformate, 92.3% diphenyl carbonate; add 20g of phenol to carry out After the heat preservation, the temperature was kept at 170° C. for 4 hours, and the measured phenyl chloroformate content was less than 0.1% as the end point. The actual molar ratio of phenol to phosgene used is 1:0.9. Using oil bath heating distillation process, the oil temperature is 180°C, the internal temperature is 150°C, and the vacuum degree is 0.086Mpa, and the phenol is distilled and separated; the oil temperature is 220°C, the internal temperature is 190°C, and the vacuum degree is 0.096Mpa, and ...
Embodiment 3
[0040] Put 282g of phenol into a 500ml reaction bottle, heat up and melt, and when it reaches 115°C, add an appropriate amount of catalyst DMF according to 1.1% of the weight of phenol. Under the condition of stirring, control the flow rate and slowly feed phosgene to ensure that the phosgene reaction is complete; the photochemical time is 11 hours, sampling analysis: phenol 5.8%, phenyl chloroformate 0.3%, diphenyl carbonate 92.3%, the reaction is over; phenol and The actual molar ratio of phosgene used is 1:0.6. Raise the temperature to 160° C. and keep it warm for 4 hours, and the measured phenyl chloroformate content is less than 0.1% as the end point. Using oil bath heating distillation process, the oil temperature is 180°C, the internal temperature is 150°C, and the vacuum degree is 0.083Mpa, and the phenol is distilled and separated; the oil temperature is 220°C, the internal temperature is 190°C, and the vacuum degree is 0.097Mpa, and the product is obtained by distill...
PUM
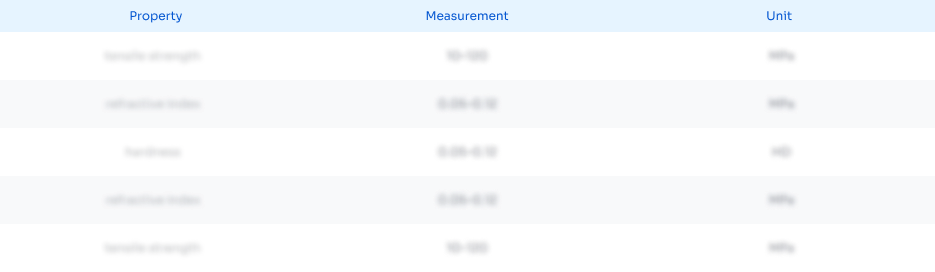
Abstract
Description
Claims
Application Information

- R&D Engineer
- R&D Manager
- IP Professional
- Industry Leading Data Capabilities
- Powerful AI technology
- Patent DNA Extraction
Browse by: Latest US Patents, China's latest patents, Technical Efficacy Thesaurus, Application Domain, Technology Topic, Popular Technical Reports.
© 2024 PatSnap. All rights reserved.Legal|Privacy policy|Modern Slavery Act Transparency Statement|Sitemap|About US| Contact US: help@patsnap.com