Prefabricated steel structural superposed shear wall and construction method thereof
A technology for superimposing shear walls and steel structures, applied in the direction of walls, building components, building structures, etc., can solve the problems of difficult implementation of prefabricated shear walls, high construction accuracy requirements, and high construction difficulties, and achieve convenient The effect of logistics and transportation, easy construction and installation, and simple construction method
- Summary
- Abstract
- Description
- Claims
- Application Information
AI Technical Summary
Problems solved by technology
Method used
Image
Examples
Embodiment 1
[0045] Refer to attached Figure 1-Figure 5 , Figure 13 and Figure 14 As shown, a prefabricated steel structure laminated shear wall, its wall panel 3 is a new type of prefabricated lightweight concrete wall panel, in the factory, polystyrene, cement, additives and water are used as raw materials, and through specialized machinery A new type of prefabrication in which the equipment is manufactured into a cement polystyrene formwork plate with horizontal and vertical holes (using it as a formwork), and self-compacting vibration-free concrete is used to form horizontal and vertical criss-cross grid members in the formwork holes. Concrete siding. The number of wall panels 3 is two, and the two wall panels 3 are anchored together by the angle steel self-locking component 1 and the self-locking component 2 2 on both sides, and there is a hollow layer between the two wall panels 3. After hoisting Concrete can be poured; each wall panel 3 is provided with multiple longitudinal g...
Embodiment 2
[0048] refer to Figure 6 and Figure 7 As shown, it is the on-site splicing process of the prefabricated steel laminated shear wall: after the previous shear wall is fixed and formed, the self-locking member 2 of the second shear wall is docked with the self-locking member 1 of the previous shear wall , docked and inserted from above, the entire wall can be automatically locked by self-locking component 1 and self-locking component 2 2, and the remaining walls are connected in sequence, and finally concrete is poured, and the high-fluidity concrete can automatically compact each wall. Thus pouring into a whole. Self-locking component 1 and self-locking component 2 2 are self-locking tools, which can clamp two wall panels 3 of a single wall to form a wall, and are also the connecting parts when the two walls are docked, and finally cast High fluidity concrete. The shear wall panel is a single-piece shell formed by pouring and molding according to certain specifications and si...
Embodiment 3
[0056] refer to Figure 8-Figure 12 As shown, the prefabricated steel structure laminated shear wall also includes the inner wall, outer wall and internal steel skeleton of the main beam - I-beam 5, which is welded by multiple T-shaped steel materials at the bottom of the web to form a ┻-shaped or ╋-shaped, as a connecting member, it can replace the structural ribs at the beams, structural columns and edge joints—that is, it is poured into a structural steel skeleton, and its flange width is based on the size of the self-locking member-1 joint, and the height and thickness of the web are based on the actual beam and slab size 1. Design of structural column stress requirements, if necessary, formwork is required to cast beam-column joints.
[0057] On-site splicing process of prefabricated steel structure laminated shear wall interior wall and exterior wall: install three pieces of shear wall on site and fix them with temporary fixing brackets. This bracket is similar to constr...
PUM
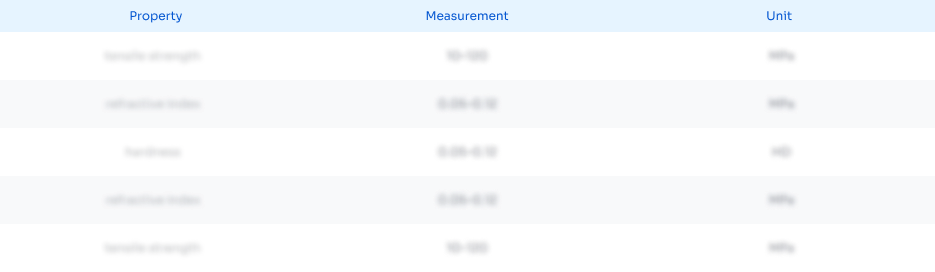
Abstract
Description
Claims
Application Information

- R&D
- Intellectual Property
- Life Sciences
- Materials
- Tech Scout
- Unparalleled Data Quality
- Higher Quality Content
- 60% Fewer Hallucinations
Browse by: Latest US Patents, China's latest patents, Technical Efficacy Thesaurus, Application Domain, Technology Topic, Popular Technical Reports.
© 2025 PatSnap. All rights reserved.Legal|Privacy policy|Modern Slavery Act Transparency Statement|Sitemap|About US| Contact US: help@patsnap.com