System and method for producing sponge iron by gas-based shaft furnace
A technology of gas-based shaft furnace and sponge iron, which is applied in the field of metallurgy, can solve the problems of reducing gas inlet blockage, reduce carbon deposition effect, and good economic benefits, so as to improve production efficiency, reduce carbon deposition effect, and economic benefits Good results
- Summary
- Abstract
- Description
- Claims
- Application Information
AI Technical Summary
Problems solved by technology
Method used
Image
Examples
Embodiment 1
[0057] Embodiment 1: The coke oven gas composition after dedusting and desulfurization is: H 2 =60%, CO=8%, CO 2 =2%, CH 4 =25%, N 2 =3%; at the same time, spray 16% of the gas volume of water vapor into the heating furnace, the heating furnace will heat the mixed gas to 1050 °C, the high-temperature gas enters the gas reforming and carburizing device for conversion, and the high-methane gas is converted into gas The composition is: H 2 =80%, CO=12.4%, CO 2 =2.2%, CH 4 =3%,N 2 =2.2%, the temperature drops to 950°C, the converted gas enters the shaft furnace reduction device to reduce iron-containing minerals, the metallization rate of the pellets reaches 95%, the carbon content is less than 0.5%, and part of the metallized pellets enters the gas The reforming and carburizing device completes carburizing, and the sponge iron with a metallization rate of 85-88% and a carbon content of 2-4% is obtained, which can be directly melted.
[0058] The temperature of the top gas ...
Embodiment 2
[0059] Embodiment two: the coke oven gas composition after dedusting and desulfurization is: H 2 =63%, CO=6%, CO 2 =4%, CH 4 =20%, N 2 =2.5%. At the same time, 12% of the gas volume water vapor is sprayed into the heating furnace. The heating furnace raises the temperature of the mixed gas to 1050°C. The high-temperature gas enters the gas reforming and carburizing device for conversion. The gas composition of the high-methane gas after conversion is: H 2 =76.7%, CO=15.8%, CO 2 =3.2%, CH 4 =2.4%, the temperature drops to 960°C, the converted gas enters the shaft furnace to reduce iron-containing minerals, the metallization rate of the pellets reaches 93%, and the carbon content is <0.3%; part of the metallized pellets enters the gas reforming And the carburizing device completes carburizing to obtain sponge iron with a metallization rate of 85-88% and a carbon content of 2-4% C%, which can be directly melted.
[0060] The temperature of the top gas produced by the reduct...
PUM
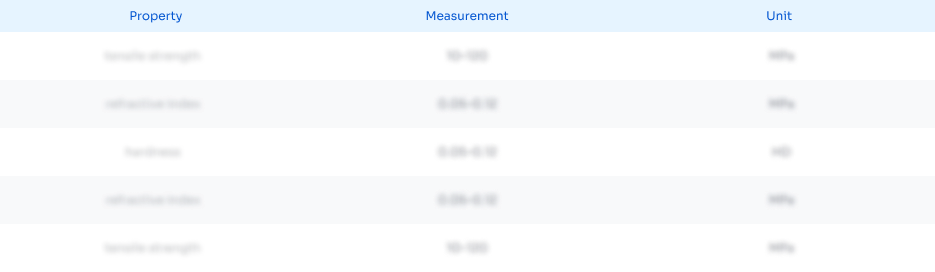
Abstract
Description
Claims
Application Information

- R&D
- Intellectual Property
- Life Sciences
- Materials
- Tech Scout
- Unparalleled Data Quality
- Higher Quality Content
- 60% Fewer Hallucinations
Browse by: Latest US Patents, China's latest patents, Technical Efficacy Thesaurus, Application Domain, Technology Topic, Popular Technical Reports.
© 2025 PatSnap. All rights reserved.Legal|Privacy policy|Modern Slavery Act Transparency Statement|Sitemap|About US| Contact US: help@patsnap.com