Method for producing silicon deoxygenation low-sulfur high-carbon steel through LF refining double slag method
A high-carbon steel and refining slag technology, applied in the field of iron and steel metallurgical molten steel refining, can solve the problems of large fluctuations in sulfur content control, unstable steel quality, and insufficient desulfurization conditions, and achieve the resolution of difficult desulfurization, improved cleanliness of molten steel, inclusions Good control effect on physical properties and plasticization
- Summary
- Abstract
- Description
- Claims
- Application Information
AI Technical Summary
Problems solved by technology
Method used
Image
Examples
Embodiment 1
[0068] This method is used to process 55SiCrA spring steel produced by an electric furnace-LF-VD-CC process flow in a certain factory. The specific implementation process is as follows:
[0069] (1) The carbon content at the end of the electric furnace is 0.14%. During the tapping process, 4kg / t low-nitrogen carbon powder is first mixed with the steel flow, and 16kg / t low-aluminum ferrosilicon and 5kg / t medium-carbon ferromanganese are added for deoxidation alloying, and Finish within 1 / 3 of the tapping amount; then add 3kg / t of lime, 5kg / t of aluminum-free refining slag, and 0.5kg / t of calcium carbide as slag materials for slag modification. When the addition is completed, strong stirring is used in the tapping process, and the amount of slag is strictly controlled during tapping; strong stirring means that the bottom blowing flow rate per 100t of steel is 400 NL / min~1000NL / min;
[0070] (2) After LF enters the station, turn on the electricity to heat, add 2kg / t low-alumina f...
Embodiment 2
[0083] This method is used for the production of 55SiCrA spring steel in a certain factory's electric furnace-LF-VD-CC process. The specific implementation process is as follows:
[0084] (1) The carbon content at the end of the electric furnace is 0.16%. During the tapping process, 3.8kg / t low-nitrogen carbon powder is mixed with the steel flow, and 17kg / t low-aluminum ferrosilicon and 5.5kg / t medium-carbon ferromanganese are added for deoxidation alloying. , and completed within 1 / 3 of the tapping amount; then add 3.5kg / t of lime, 5kg / t of aluminum-free refining slag, and 0.4kg / t of calcium carbide as slag materials for slag modification. Adding is completed at 4 / 5, strong stirring is adopted in the tapping process, and the amount of slag is strictly controlled during tapping; strong stirring means that the bottom blowing flow rate per 100t of steel is 400 NL / min~1000NL / min;
[0085] (2) After the LF enters the station, turn on the electricity to heat, add 1.5kg / t low-alumi...
Embodiment 3
[0098] For the preparation of hard wire steel or cord steel, it is also applicable to the LF refining double slag method in this embodiment to produce silicon deoxidized low sulfur hard wire steel or cord steel, because the chemical composition of hard wire steel or cord steel is different, so In the processes of deoxidation alloying treatment, upgrading treatment, high-basic reducing refining slag and low-basic reducing refining slag, the addition amount of each component is not the same.
PUM
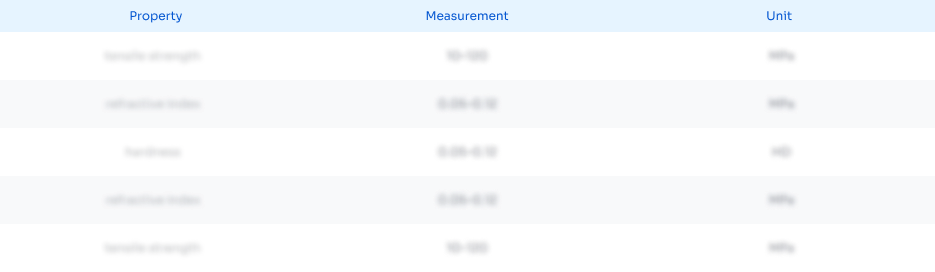
Abstract
Description
Claims
Application Information

- R&D
- Intellectual Property
- Life Sciences
- Materials
- Tech Scout
- Unparalleled Data Quality
- Higher Quality Content
- 60% Fewer Hallucinations
Browse by: Latest US Patents, China's latest patents, Technical Efficacy Thesaurus, Application Domain, Technology Topic, Popular Technical Reports.
© 2025 PatSnap. All rights reserved.Legal|Privacy policy|Modern Slavery Act Transparency Statement|Sitemap|About US| Contact US: help@patsnap.com