Water-resistant inorganic zinc-rich coating and preparation technology thereof
An inorganic zinc-rich coating and water resistance technology, applied in anti-corrosion coatings, alkali metal silicate coatings, coatings, etc., can solve the problems of slow curing speed, poor water resistance, and inability to form films in time, and improve early water resistance. , the effect of uniform particle size distribution
- Summary
- Abstract
- Description
- Claims
- Application Information
AI Technical Summary
Problems solved by technology
Method used
Examples
Embodiment 1
[0028] In the present embodiment, the high-performance water-based inorganic zinc-rich paint comprises the following components:
[0029] Potassium silicate solution 10%
[0030] water 20%
[0031] Aluminum modified silica sol 34.5%
[0032] Trimethylbenzyl ammonium hydroxide catalyst 0.5%
[0033] Lauryl Glycolamide 5%
[0034] Silane coupling agent 5%
[0035] Silicone acrylic emulsion 5%
[0036] Low lead zinc powder 19%
[0037] Potassium zirconium carbonate hardener 1%.
[0038] The preparation method of above-mentioned waterborne inorganic zinc-rich paint comprises the steps:
[0039] (1) Take 100g of potassium silicate solution with a percentage concentration of 3% and pour it into a container, add 200g of water and stir, and heat up to 50°C;
[0040] (2) Then add 5g of trimethylbenzyl ammonium hydroxide catalyst, stir and reflux for 4h;
[0041] (3) Slowly add 345 g of aluminum-modified silica sol with a molar content of 0.5% dropwise, and stir and reflux for ...
Embodiment 2
[0045] In the present embodiment, the high-performance water-based inorganic zinc-rich paint comprises the following components:
[0046] Potassium silicate solution 20%
[0047] water 15%
[0048] Aluminum modified silica sol 30%
[0049] Trimethylbenzyl ammonium hydroxide catalyst 2%
[0050] Lauryl Glycolamide 10%
[0051] Silane coupling agent 8%
[0052] Silicone acrylic emulsion 5%
[0053] Low lead zinc powder 9%
[0054] Potassium zirconium carbonate hardener 1%.
[0055] The preparation method of above-mentioned waterborne inorganic zinc-rich paint comprises the steps:
[0056] (1) Take 1000g of potassium silicate solution with a percentage concentration of 4% and pour it into a container, add 750g of water to stir, and heat up to 70°C;
[0057] (2) Finally, add 100g of trimethylbenzyl ammonium hydroxide catalyst, stir and reflux for 3h;
[0058] (3) Slowly add 1500 g of aluminum-modified silica sol with a molar content of 1%, stirring and refluxing for 3 hou...
Embodiment 3
[0062] In the present embodiment, the high-performance water-based inorganic zinc-rich paint comprises the following components:
[0063] Potassium silicate solution 10%
[0064] water 15%
[0065] Aluminum modified silica sol 40%;
[0066] Trimethylbenzyl ammonium hydroxide catalyst 3%
[0067] Lauryl Glycolamide 5%
[0068] Silane coupling agent 7%
[0069] Silicone acrylic emulsion 10%
[0070] Low lead zinc powder 9.4%
[0071] Potassium zirconium carbonate hardener 0.6%.
[0072] The preparation method of above-mentioned waterborne inorganic zinc-rich paint comprises the steps:
[0073](1) Take 5000g of potassium silicate solution with a percentage concentration of 5% and pour it into a container, add 7500g of water to stir, and heat up to 60°C;
[0074] (2) Then add 1500g of trimethylbenzyl ammonium hydroxide catalyst, stir and reflux for 3h;
[0075] (3) Slowly add 20,000 g of aluminum-modified silica sol with a molar content of 2% dropwise, and stir and reflux...
PUM
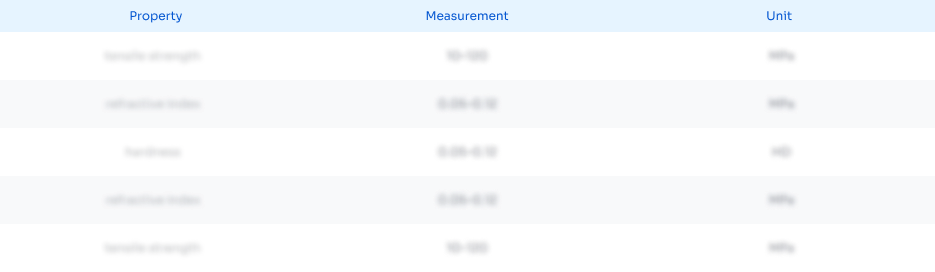
Abstract
Description
Claims
Application Information

- R&D
- Intellectual Property
- Life Sciences
- Materials
- Tech Scout
- Unparalleled Data Quality
- Higher Quality Content
- 60% Fewer Hallucinations
Browse by: Latest US Patents, China's latest patents, Technical Efficacy Thesaurus, Application Domain, Technology Topic, Popular Technical Reports.
© 2025 PatSnap. All rights reserved.Legal|Privacy policy|Modern Slavery Act Transparency Statement|Sitemap|About US| Contact US: help@patsnap.com