A kind of manufacturing method of tension screw type laminated iron core
A technology of tightening screw and manufacturing method, which is applied in the manufacturing field of laminated iron cores, can solve problems such as easy reduction of compression degree, failure to eliminate stress, and damage to coil insulation, so as to avoid local heating, reduce production costs, and improve electrical performance. performance effect
- Summary
- Abstract
- Description
- Claims
- Application Information
AI Technical Summary
Problems solved by technology
Method used
Image
Examples
Embodiment 1
[0039] Embodiment one, see appendix figure 1 , the present invention tension screw type outer pressure-mounted stator iron core 1 uses a kind of manufacture method of iron core of the present invention, and it comprises the following steps:
[0040] Step 1. Stretch the screw-type external press-fit stator core 1 and stack the iron core punching pieces I2, install the tensioning screw I3, apply axial segmental pressure to the stator core 1, and stack the iron core punching pieces I2 And after the pressure is applied, in the compressed state, preliminarily tighten the fastening element of the tension screw I3 of the tension screw type outer press-fit stator core 1: nut I4;
[0041] Step 2, compaction treatment, that is, perform compaction treatment on the preliminarily tightened tension screw type external press-fit stator core 1;
[0042] Step 3. When the iron core is at normal temperature, re-tighten the tension screw Ⅰ3 of the tension screw type external press-fit stator cor...
Embodiment 2
[0048] Embodiment two, see appendix figure 1 , the present invention tension screw type outer pressure-mounted stator iron core 1 uses a kind of manufacture method of iron core of the present invention, and it comprises the following steps:
[0049] Step 1. Stretch the screw-type external press-fit stator core 1 and stack the iron core punching pieces I2, install the tensioning screw I3, apply axial segmental pressure to the stator core 1, and stack the iron core punching pieces I2 And after the pressure is applied, in the compressed state, preliminarily tighten the fastening element of the tension screw I3 of the tension screw type outer press-fit stator core 1: nut I4;
[0050] Step 2, compaction treatment, that is, perform compaction treatment on the preliminarily tightened tension screw type external press-fit stator core 1;
[0051] Step 3. When the iron core is at normal temperature, re-tighten the tension screw Ⅰ3 of the tension screw type external press-fit stator cor...
Embodiment 3
[0057] Embodiment three, referring to the attached figure 2 , embodiment 2 tightening screw rod type internal press-fit stator iron core 6 uses a kind of manufacturing method of iron core of the present invention, and it comprises the following steps:
[0058] Step 1. In the machine base 7, stack the iron core punching sheet II 8 of the tension screw type internal press-fit stator core 6, install the tension screw II 9, and apply axial segmental pressure to the stator iron core 6, After the iron core punching sheet Ⅱ8 is stacked and pressed, in the compacted state, preliminarily tighten the tightening element of the tension screw Ⅱ9 of the tension screw type inner press-fit stator core 6: nut Ⅱ10;
[0059] Step 2, compaction treatment, that is, perform compaction treatment on the preliminarily tightened tension screw type internal press-fit stator core 6;
[0060] Step 3. When the iron core is at room temperature, re-tighten the tightening screw II 9 of the tightened screw-t...
PUM
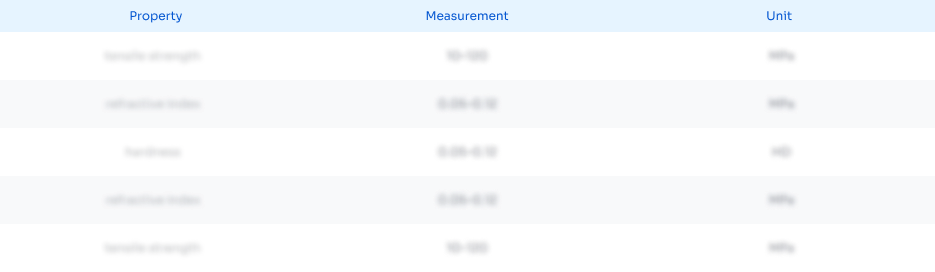
Abstract
Description
Claims
Application Information

- R&D
- Intellectual Property
- Life Sciences
- Materials
- Tech Scout
- Unparalleled Data Quality
- Higher Quality Content
- 60% Fewer Hallucinations
Browse by: Latest US Patents, China's latest patents, Technical Efficacy Thesaurus, Application Domain, Technology Topic, Popular Technical Reports.
© 2025 PatSnap. All rights reserved.Legal|Privacy policy|Modern Slavery Act Transparency Statement|Sitemap|About US| Contact US: help@patsnap.com