Graphene coating master batch and preparation method
A graphene and coating technology, applied in chemical instruments and methods, fibrous fillers, inorganic pigment processing, etc., can solve the problems of continuous and stable large-scale production, poor dispersion effect, and long time-consuming masterbatch, reaching a significant market. Application value, improved compatibility, low cost effect
- Summary
- Abstract
- Description
- Claims
- Application Information
AI Technical Summary
Problems solved by technology
Method used
Image
Examples
Embodiment 1
[0032] (1) Disperse 5 parts of graphene oxide in 42 parts of solution in parts by mass. The solvent is deionized water dissolved with 2 parts by mass of dispersant cetyltrimethylammonium bromide, and the molar concentration Mix 10-20 parts of copper sulfate aqueous solution of 7mol / L, ultrasonically disperse, and the power of ultrasonically disperse is 8kW, obtain the copper ion surface-modified graphene oxide dispersion solution, the copper ion surface-modified graphene oxide dispersion solution The solution is heated and the temperature is controlled to be 50°C;
[0033](2) The copper ion surface-modified graphene oxide dispersion solution is mixed with a phenolic resin emulsion with a solid content of 50% in a mass ratio of 1:0.6, and the ultrasonic dispersion power is set to 5kW for further ultrasonic dispersion, Obtain the modified graphene oxide dispersion solution wrapped in resin;
[0034] (3) The ratio of the mass of sodium borohydride to graphene oxide is 1:1.2. Whe...
Embodiment 2
[0036] (1) Disperse 10 parts of graphene oxide in 40 parts of solution according to the number of parts by mass. The solvent is deionized water dissolved with 2 parts by mass of sodium dodecylbenzenesulfonate, and the molar concentration is 8mol / L 10 parts of copper sulfate aqueous solution are mixed, ultrasonically dispersed, and the power of ultrasonic dispersion is 8kW, obtains the graphene oxide dispersion solution of copper ion surface modification, the graphene oxide dispersion solution of described copper ion surface modification is heated, controls temperature 70°C;
[0037] (2) The copper ion surface-modified graphene oxide dispersion solution is mixed with a styrene-acrylic emulsion with a solid content of 50% in a mass ratio of 1:0.5, and further ultrasonically dispersed. The power of ultrasonic dispersion is 8kW, and the obtained Resin-wrapped modified graphene oxide dispersion solution;
[0038] (3) The ratio of the mass of sodium borohydride to graphene oxide is...
Embodiment 3
[0040] (1) Disperse 2 parts of graphene oxide in 40 parts of solution according to the number of parts by mass. The solvent is deionized water dissolved with 1 part by mass of polyvinyl alcohol and polyethylene composition, and the molar concentration is 6mol / L 10 parts of copper sulfate aqueous solution are mixed, ultrasonic dispersion, the power of ultrasonic dispersion is 4kW, obtain the graphene oxide dispersion solution of copper ion surface modification, the graphene oxide dispersion solution of described copper ion surface modification is heated, control temperature 65°C;
[0041] (2) The copper ion surface-modified graphene oxide dispersion solution is mixed with a phenolic resin emulsion with a solid content of 50% in a mass ratio of 1:0.8, and further ultrasonically dispersed, and the power of ultrasonic dispersion is 3kW, to obtain Resin-wrapped modified graphene oxide dispersion solution;
[0042] (3) The ratio of the mass of sodium borohydride to graphene oxide i...
PUM
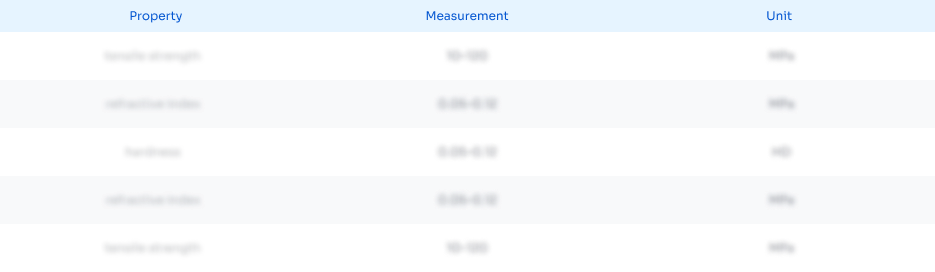
Abstract
Description
Claims
Application Information

- R&D
- Intellectual Property
- Life Sciences
- Materials
- Tech Scout
- Unparalleled Data Quality
- Higher Quality Content
- 60% Fewer Hallucinations
Browse by: Latest US Patents, China's latest patents, Technical Efficacy Thesaurus, Application Domain, Technology Topic, Popular Technical Reports.
© 2025 PatSnap. All rights reserved.Legal|Privacy policy|Modern Slavery Act Transparency Statement|Sitemap|About US| Contact US: help@patsnap.com