Machining process for bladed full-PCD milling cutter
A processing technology and milling cutter technology, which is applied in the field of full PCD milling cutter processing technology, can solve the problems of difficulty in ensuring accuracy, high cost, and difficulty in processing PCD materials, and achieve the effect of ensuring consistency and preventing wear and deformation
- Summary
- Abstract
- Description
- Claims
- Application Information
AI Technical Summary
Problems solved by technology
Method used
Examples
Embodiment Construction
[0013] In order to deepen the understanding of the present invention, the present invention will be further described below in conjunction with the examples, which are only used to explain the present invention, and do not constitute a limitation to the protection scope of the present invention.
[0014] This embodiment provides a process for processing a full PCD milling cutter with a margin, and the full PCD milling cutter with a margin includes the following processing steps:
[0015] Step 1: Use a tool grinder to grind a notch on the PCD base metal near the PCD part, and then measure the angle difference between the notch and the A-axis of the PCD part on the tool detector to determine the reference position for processing;
[0016] Step 2: Electrolytic grooving, using a diamond grinding wheel to perform rough grooving on the PCD base material, and then using a copper wheel for electrolytic fine grooving;
[0017] Step 3: Electrolytic chip flutes, end teeth chip flutes are...
PUM
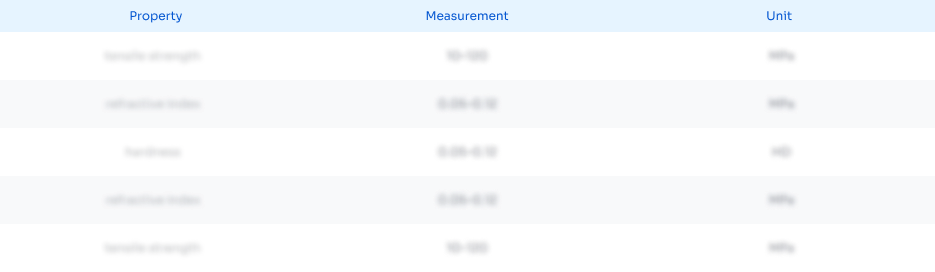
Abstract
Description
Claims
Application Information

- Generate Ideas
- Intellectual Property
- Life Sciences
- Materials
- Tech Scout
- Unparalleled Data Quality
- Higher Quality Content
- 60% Fewer Hallucinations
Browse by: Latest US Patents, China's latest patents, Technical Efficacy Thesaurus, Application Domain, Technology Topic, Popular Technical Reports.
© 2025 PatSnap. All rights reserved.Legal|Privacy policy|Modern Slavery Act Transparency Statement|Sitemap|About US| Contact US: help@patsnap.com