Preparation method for electrohydrodynamic jet deposition and laser cladding microtexture tool
A technology of laser cladding and micro-texture, which is applied in the coating process and coating of metal materials, can solve the problems of complex tool texture process and high cost, and achieve rapid and reliable solidification molding, small thermal deformation of materials, and texture structure. The effect of high precision
- Summary
- Abstract
- Description
- Claims
- Application Information
AI Technical Summary
Problems solved by technology
Method used
Image
Examples
example 1
[0027] A preparation method of electro-jet deposition-laser cladding micro-textured tool, the base material is W18Cr4V high-speed steel tool, and the micro-textured material is Al 2 o 3 (its main component is 97% Al 2 o 3 , 2% Ni and 1% Al). It is characterized in that micro-texture is processed on the rake face of the tool. Concrete preparation process steps are as follows:
[0028] (1) Pretreatment of the tool substrate
[0029] The surface of the W18Cr4V high-speed steel tool was polished, and ultrasonically cleaned in acetone and absolute ethanol solutions for 20 min in order to remove the dirt on the tool surface.
[0030] (2) Electrojet deposition of microtexture
[0031] The computer 5 draws a three-dimensional model of the micro-texture, and uses the cross-sectional profile data and filling data of each layer of the three-dimensional model to generate the motion path and speed of the three-dimensional motion platform substrate 7 corresponding to the micro-texture...
example 2
[0036] A preparation method of electro-jet deposition-laser cladding micro-textured tool, the base material is W6Mo5Cr4V2 high-speed steel tool, the micro-textured material is hard alloy (the main components are 80% WC, 10% Co, 5% W, 1.5%VC, 1%Cr 3 C 2 and 1% Ni, 1% Al and 0.5% Mo). It is characterized in that micro-texture is processed on the rake face of the tool. Concrete preparation process steps are as follows:
[0037] (1) Pretreatment of the tool substrate
[0038] The surface of the W6Mo5Cr4V2 high-speed steel tool was polished, and then put into acetone and absolute ethanol solution for ultrasonic cleaning for 20 minutes to remove the dirt on the tool surface.
[0039] (2) Electrojet deposition of microtexture
[0040] The computer 5 draws a three-dimensional model of the micro-texture, and generates the motion path and speed of the three-dimensional motion platform substrate 7 corresponding to the micro-texture by using the cross-sectional profile data and filli...
PUM
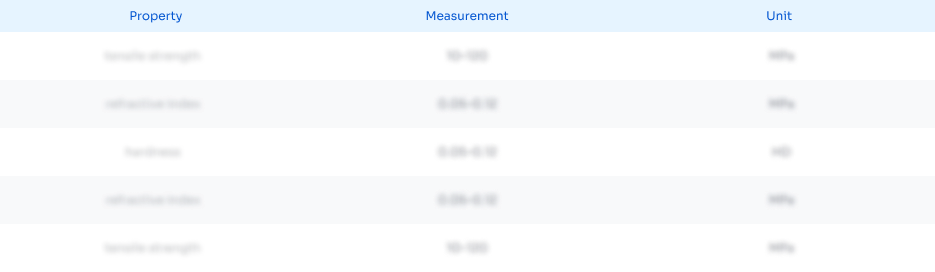
Abstract
Description
Claims
Application Information

- R&D Engineer
- R&D Manager
- IP Professional
- Industry Leading Data Capabilities
- Powerful AI technology
- Patent DNA Extraction
Browse by: Latest US Patents, China's latest patents, Technical Efficacy Thesaurus, Application Domain, Technology Topic, Popular Technical Reports.
© 2024 PatSnap. All rights reserved.Legal|Privacy policy|Modern Slavery Act Transparency Statement|Sitemap|About US| Contact US: help@patsnap.com