A kind of method for preparing isobutene
A technology of isobutene and main reactor, applied in ether preparation, chemical instruments and methods, unsaturated compound addition to prepare ether, etc., can solve the problems of secondary reaction of isobutene, influence of device operation cycle, untimely gas-liquid separation, etc.
- Summary
- Abstract
- Description
- Claims
- Application Information
AI Technical Summary
Problems solved by technology
Method used
Image
Examples
Embodiment 1
[0040] A kind of method for preparing isobutylene, under the action of molecular sieve catalyst, glycol ether is catalytically cracked in fluidized bed, and this technique is realized by following device:
[0041] The device comprises a fluidized bed cracking main reactor (R104), and the deactivated catalyst outlet (202) at the bottom of the fluidized bed cracking main reactor (R104) is connected with the deactivated catalyst regeneration tank (D103), The upper part of bed cracking main reactor (R104) is provided with fresh catalyst inlet (203), and described fresh catalyst inlet (203) links to each other with deactivated catalyst regeneration tank (D103), and described fluidized bed cracking main reactor (R104 ) bottom is also provided with a raw material inlet (201), and the top of the fluidized bed cracking main reactor (R104) is provided with a gas production outlet (204), and the gas production outlet (204) is connected with the gas-liquid separation tank (V106) The gas-l...
Embodiment 2
[0046] The raw material is 97% ethylene glycol mono-tert-butyl ether, and the active component is ZSM-5 silica gel particle molecular sieve as the catalyst. figure 1 In the process flow shown, 25kg of activated catalyst is loaded into the regeneration tank, the preheating temperature of the raw material is 190°C, the raw material is heated to 220°C through the heater, and the external heat collector is adjusted from the feed pipe distributor into the main reactor. The reaction temperature is controlled at 210°C, the residence time of the gas phase in the dense phase catalyst bed is about 1.5s, the reaction gas enters the condenser through the top of the tower and is cooled to 60°C and enters the gas-liquid separation tank, and the liquid phase in the gas-liquid separation tank The diol enters the ethylene glycol refining tower, and the gas phase enters the isobutene gas production buffer tank. The catalyst in the regenerator is burnt in the air, and the regeneration temperature...
Embodiment 3
[0048] With the content of 56% ethylene glycol mono-tert-butyl ether and 44% ethylene glycol di-tert-butyl ether as raw material, the active component is ZSM-5 silica gel particle molecular sieve as catalyst, using figure 1 In the process flow shown, 25kg of activated catalyst is loaded into the regeneration tank, the preheating temperature of the raw material is 190°C, and the raw material is heated to 250°C through a heater. Enter the main reactor from the tubular feed distributor, adjust the external heat collector, control the reaction temperature to be 210 and 240°C respectively, the residence time of the gas phase in the dense phase catalyst bed is about 1.5s, and the reaction gas enters through the top of the tower The condenser is cooled to 60°C and enters the gas-liquid separation tank. The liquid phase in the gas-liquid separation tank enters the ethylene glycol light removal tower, and the gas phase enters the isobutene gas production buffer tank. The catalyst in the...
PUM
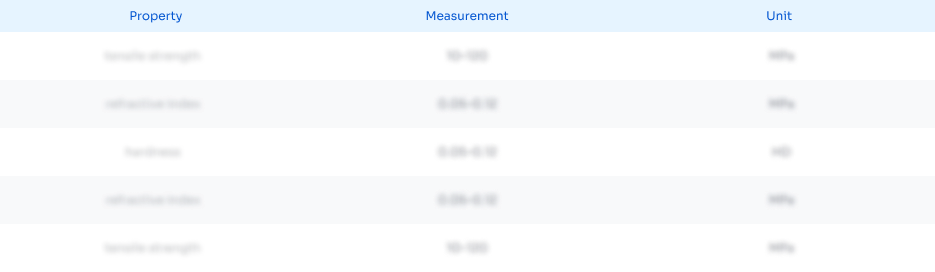
Abstract
Description
Claims
Application Information

- Generate Ideas
- Intellectual Property
- Life Sciences
- Materials
- Tech Scout
- Unparalleled Data Quality
- Higher Quality Content
- 60% Fewer Hallucinations
Browse by: Latest US Patents, China's latest patents, Technical Efficacy Thesaurus, Application Domain, Technology Topic, Popular Technical Reports.
© 2025 PatSnap. All rights reserved.Legal|Privacy policy|Modern Slavery Act Transparency Statement|Sitemap|About US| Contact US: help@patsnap.com