Method of smelting low-aluminum medium ferrovanadium by means of tilting furnace
A tilting furnace and ferro-vanadium technology, which is applied in the field of metallurgy, can solve problems such as substandard product quality and difficult control of alloy aluminum content, and achieve the effects of increasing smelting yield, reducing vanadium content, and improving economic benefits
- Summary
- Abstract
- Description
- Claims
- Application Information
AI Technical Summary
Problems solved by technology
Method used
Examples
Embodiment 1
[0021] The raw materials vanadium oxide, aluminum, iron and lime are mixed and put into a tiltable electric arc furnace for smelting in three phases. The aluminum ratio in the first two phases is 1.10, and the raw material in the first phase is: flake vanadium (V 2 o 5 Mass content 98.0%) 1000kg, V 2 o 3 3000kg (containing 64.0% vanadium), with 1922kg of aluminum, 2276kg of iron and 600kg of lime. After mixing the material evenly, put it into the furnace. The secondary voltage is 190V to energize the arc. Slag 3550kg; then add the second phase of raw materials: V 2 o 3 3000kg (containing 64.0% vanadium), with 1375kg of aluminum, 1707kg of iron, and 450kg of lime; after the charge is cleared, the secondary voltage is selected as 150V. After smelting and electrifying for 40 minutes, the residual vanadium in the slag is quickly analyzed to be 0.75%, and the theoretical slag in the furnace is 3900kg. Slag 3100kg; then add the third phase of raw materials: Fe 2 o 3(98.3%) 50...
Embodiment 2
[0023] The raw materials of vanadium oxide, aluminum, iron and lime are mixed and put into a tiltable electric arc furnace for smelting in three stages. The aluminum ratio of the first two stages is: 1.15, and the raw material of the first stage is: flake vanadium (V 2 o 5 Mass content 98.2%) 1000kg, V 2 o 3 3000kg (containing 64.2% vanadium), with 2009kg of aluminum, 2282kg of iron and 600kg of lime. Mix the material evenly and put it into the furnace. The secondary voltage is 190V to energize and start the arc. After the furnace material is cleared, the secondary voltage is 150V. After smelting and electrifying for 90 minutes, the residual vanadium in the slag was quickly analyzed to be 0.25%, the theoretical slag amount in the furnace was 4400kg, and the slag output was 3620kg; after that, the second phase of raw materials was added: V 2 o 3 3000kg (containing 64.4% of vanadium), 1437kg of aluminum, 1587kg of iron, 450kg of lime; after the charge is cleared, the seconda...
Embodiment 3
[0025] The raw materials of vanadium oxide, aluminum, iron and lime are mixed and put into a tiltable electric arc furnace for smelting in three stages. The aluminum ratio of the first two stages is: 1.20, and the raw material of the first stage is: flake vanadium (V 2 o 5 Mass content 98.2%) 1000kg, V 2 o 3 3000kg (containing 64.8% vanadium), with 2096kg of aluminum, 2272kg of iron and 600kg of lime. Mix the material evenly and put it into the furnace. The secondary voltage is 190V to energize and start the arc. After the furnace material is cleared, the secondary voltage is 150V. After 90 minutes of smelting and electrification, the residual vanadium in the slag was quickly analyzed to be 0.15%, the theoretical slag amount in the furnace was 4400kg, and the slag output was 3650kg; after that, the second phase of raw materials was added: V 2 o 3 3000kg (containing 64.6% of vanadium), 1500kg of aluminum, 1275kg of iron, 450kg of lime; the secondary voltage after the charge...
PUM
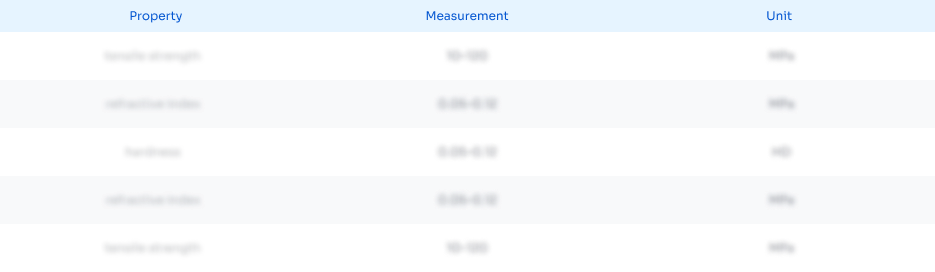
Abstract
Description
Claims
Application Information

- R&D
- Intellectual Property
- Life Sciences
- Materials
- Tech Scout
- Unparalleled Data Quality
- Higher Quality Content
- 60% Fewer Hallucinations
Browse by: Latest US Patents, China's latest patents, Technical Efficacy Thesaurus, Application Domain, Technology Topic, Popular Technical Reports.
© 2025 PatSnap. All rights reserved.Legal|Privacy policy|Modern Slavery Act Transparency Statement|Sitemap|About US| Contact US: help@patsnap.com