Method for preparing ferrovanadium by electric aluminotherm method in tilting furnace
An electric thermite and tilting furnace technology, applied in the field of metallurgy, can solve the problems of saving aluminum consumption and improving the smelting yield of vanadium and iron, so as to reduce the aluminum consumption of a single furnace, reduce the vanadium content, and increase the smelting yield Effect
- Summary
- Abstract
- Description
- Claims
- Application Information
AI Technical Summary
Problems solved by technology
Method used
Examples
Embodiment 1
[0025] The raw materials vanadium oxide, aluminum, iron and lime that meet the production requirements are mixed and put into a tiltable electric arc furnace for smelting in three phases. The aluminum ratio is A:B:C=1.4:0.7:0.5, (A *4+B*2+C*2) / 8=1, Phase 1 raw material: flake vanadium (V 2 o 5 Mass content 98.0%) 1000kg, V 2 o 3 3000kg (containing 64.1% vanadium), with 2446kg of aluminum, 2276kg of iron and 600kg of lime. Mix the material evenly and put it into the furnace. The secondary voltage is 190V to energize and start the arc. After the furnace material is cleared, the secondary voltage is 135V. After smelting and electrifying for 90 minutes, the residual vanadium in the slag was quickly analyzed to be 0.12%, the theoretical slag amount in the furnace was 4400kg, and the slag output was 3550kg; after that, the second phase raw material was added: V 2 o 3 2000kg (containing 64.5% of vanadium), with 588kg of aluminum, 1138kg of iron, and 300kg of lime; after the furn...
Embodiment 2
[0028] The raw materials vanadium oxide, aluminum, iron and lime that meet the production requirements are mixed and put into a tiltable electric arc furnace for smelting in three phases. The ratio of aluminum ratio is A:B:C=1.25:0.95:0.65, (A *4+B*2+C*2) / 8=1, Phase 1 raw material: flake vanadium (V 2 o 5 Mass content 98.2%) 1000kg, V 2 o 3 3000kg (containing 64.2% vanadium), with 2168kg of aluminum, 2282kg of iron and 600kg of lime. Mix the material evenly and put it into the furnace. The secondary voltage is 190V to energize and start the arc. After the furnace material is cleared, the secondary voltage is 135V. After smelting and electrifying for 90 minutes, the residual vanadium in the slag was quickly analyzed to be 0.25%, the theoretical slag amount in the furnace was 4400kg, and the slag output was 3620kg; after that, the second phase raw material: V 2 o 3 2000kg (containing 64.4% of vanadium), with 778kg of aluminum, 1140kg of iron, and 300kg of lime; after the fu...
Embodiment 3
[0031] The raw materials vanadium oxide, aluminum, iron and lime that meet the production requirements are mixed and put into a tiltable electric arc furnace for smelting in three phases. The aluminum ratio is A:B:C=1.4:1:0.2, (A *4+B*2+C*2) / 8=1, Phase 1 raw material: flake vanadium (V 2 o 5 Mass content 98.2%) 1000kg, V 2 o 3 3000kg (containing 64.8% vanadium), with 2445kg of aluminum, 2272kg of iron and 600kg of lime. Mix the material evenly and put it into the furnace. The secondary voltage is 190V to energize and start the arc. After the furnace material is cleared, the secondary voltage is 135V. After the smelting was electrified for 90 minutes, the residual vanadium in the slag was quickly analyzed to be 0.15%, the theoretical slag amount in the furnace was 4400kg, and the slag output was 3650kg; after that, the second phase raw material was added: V 2 o 3 2000kg (containing 64.6% of vanadium), 852kg of aluminum, 1135kg of iron, 300kg of lime; the secondary voltage ...
PUM
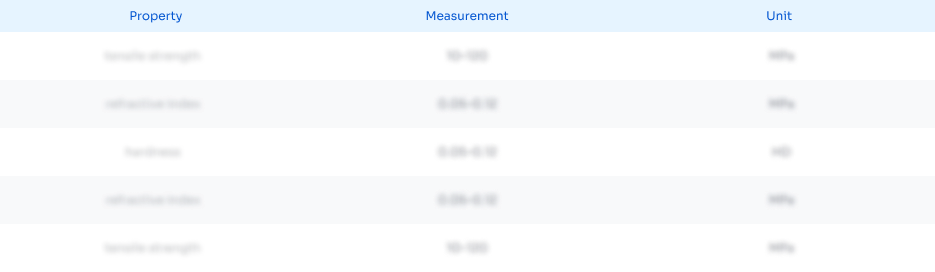
Abstract
Description
Claims
Application Information

- R&D Engineer
- R&D Manager
- IP Professional
- Industry Leading Data Capabilities
- Powerful AI technology
- Patent DNA Extraction
Browse by: Latest US Patents, China's latest patents, Technical Efficacy Thesaurus, Application Domain, Technology Topic, Popular Technical Reports.
© 2024 PatSnap. All rights reserved.Legal|Privacy policy|Modern Slavery Act Transparency Statement|Sitemap|About US| Contact US: help@patsnap.com