Method for evenly prolonging service life of electric furnace used for smelting ferrovanadium by electro-silicothermic process
An electrosilicon thermal method and balanced extension technology, which is applied in the field of ferro-vanadium metallurgy production, can solve the problems of furnace mud not being bonded, loss of protection, penetration, floating, etc., to increase the output of a single furnace, reduce the consumption, and extend the The effect of furnace age
- Summary
- Abstract
- Description
- Claims
- Application Information
AI Technical Summary
Problems solved by technology
Method used
Image
Examples
Embodiment 1
[0031] Example 3: Using a 3t electric arc furnace, spread 200kg of a mixture of trivalent vanadium oxide and tetravalent vanadium oxide evenly on the bottom of the electric furnace before smelting, then add scrap steel, reheated fine slag, and add raw and auxiliary materials according to the proportion For ferrovanadium smelting, because the mixture of trivalent vanadium oxide and tetravalent vanadium oxide at the bottom of the furnace has a high melting point, it gradually participates in the reaction during the smelting process, and a protective layer can be formed on the bottom of the furnace to protect the bottom of the furnace. The age is increased to 148 furnaces.
Embodiment 2
Embodiment 3
PUM
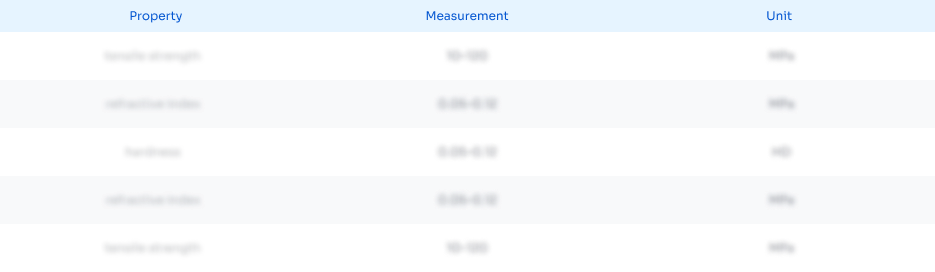
Abstract
Description
Claims
Application Information

- Generate Ideas
- Intellectual Property
- Life Sciences
- Materials
- Tech Scout
- Unparalleled Data Quality
- Higher Quality Content
- 60% Fewer Hallucinations
Browse by: Latest US Patents, China's latest patents, Technical Efficacy Thesaurus, Application Domain, Technology Topic, Popular Technical Reports.
© 2025 PatSnap. All rights reserved.Legal|Privacy policy|Modern Slavery Act Transparency Statement|Sitemap|About US| Contact US: help@patsnap.com