Production method of polytetrafluoroethylene film
A technology of polytetrafluoroethylene and its production method, which is applied in the field of chemical materials and can solve problems such as unreasonable process conditions, uneven products, and insufficient density
- Summary
- Abstract
- Description
- Claims
- Application Information
AI Technical Summary
Problems solved by technology
Method used
Examples
Embodiment 1
[0014] The production method of the polytetrafluoroethylene film of the present embodiment may further comprise the steps:
[0015] A, take by weight 75 parts of polytetrafluoroethylene, 15 parts of polyacrylamide, 7 parts of calcium carbonate, 1 part of silicon dioxide, 6 parts of polyurethane, and 13 parts of polyimide are put into the reactor;
[0016] B. Introduce nitrogen into the reactor and heat for 20 minutes, the heating temperature is 170°C, then weigh 2 parts of glass fiber, 3 parts of talcum powder, and 1 part of carbon black by weight and put them into the reactor to continue heating and reaction for 40 minutes minutes, the heating temperature is 230°C;
[0017] C. Feed the reacted mixture into the twin-screw extruder through the constant temperature hopper for processing, and the temperature of the constant temperature hopper is controlled at 75°C;
[0018] D. The twin-screw extruded strips of the twin-screw extruder are air-cooled and then water-cooled in the t...
Embodiment 2
[0020] The production method of the polytetrafluoroethylene film of the present embodiment may further comprise the steps:
[0021] A, take by weight 80 parts of polytetrafluoroethylene, 17 parts of polyacrylamide, 9 parts of calcium carbonate, 1 part of silicon dioxide, 7 parts of polyurethane, and 14 parts of polyimide and put them into the reactor;
[0022] B. Feed nitrogen gas into the reactor and heat for 25 minutes. The heating temperature is 190°C. Then weigh 3 parts of glass fiber, 4 parts of talcum powder and 1 part of carbon black by weight and put them into the reactor to continue heating and reacting for 50 minutes. minutes, the heating temperature is 240°C;
[0023] C. Feed the reacted compound into the twin-screw extruder through the constant temperature hopper for processing, and the temperature of the constant temperature hopper is controlled at 77°C;
[0024] D. The twin-screw extruded strips of the twin-screw extruder are air-cooled and then water-cooled in ...
Embodiment 3
[0026] The production method of the polytetrafluoroethylene film of the present embodiment may further comprise the steps:
[0027] A, take by weight 95 parts of polytetrafluoroethylene, 18 parts of polyacrylamide, 10 parts of calcium carbonate, 2 parts of silicon dioxide, 8 parts of polyurethane, and 15 parts of polyimide are put into the reactor;
[0028] B. Feed nitrogen into the reactor and heat for 30 minutes, the heating temperature is 210°C, then weigh 3 parts of glass fiber, 5 parts of talcum powder, and 2 parts of carbon black by weight and put them into the reactor to continue heating and reacting for 60 minutes, the heating temperature is 250°C;
[0029] C. Send the reacted mixture into the twin-screw extruder through the constant temperature hopper for processing, and the temperature of the constant temperature hopper is controlled at 80°C;
[0030] D. The twin-screw extruded strip of the twin-screw extruder is air-cooled and then water-cooled in the temperature c...
PUM
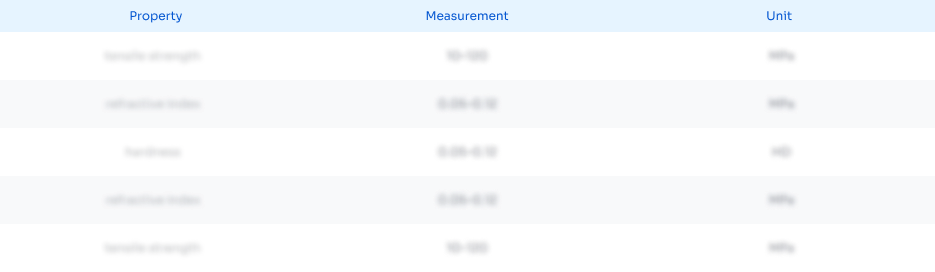
Abstract
Description
Claims
Application Information

- Generate Ideas
- Intellectual Property
- Life Sciences
- Materials
- Tech Scout
- Unparalleled Data Quality
- Higher Quality Content
- 60% Fewer Hallucinations
Browse by: Latest US Patents, China's latest patents, Technical Efficacy Thesaurus, Application Domain, Technology Topic, Popular Technical Reports.
© 2025 PatSnap. All rights reserved.Legal|Privacy policy|Modern Slavery Act Transparency Statement|Sitemap|About US| Contact US: help@patsnap.com