PCB lamination and fusion anti-wrinkling method
A technology of PCB board and pressing machine, which is applied in the manufacturing of multi-layer circuits, electrical components, printed circuits, etc., can solve the problems of poor bonding force in the fusion area, unreasonable process methods, and layer deviation after pressing, so as to avoid The effect of wrinkling extension, avoiding copper foil wrinkling and increasing bonding force
- Summary
- Abstract
- Description
- Claims
- Application Information
AI Technical Summary
Problems solved by technology
Method used
Examples
Embodiment Construction
[0018] A PCB lamination fusion anti-wrinkle method provided by an embodiment of the present invention includes the following steps:
[0019] S1: Stacking boards, stacking and fixing each layer of boards required to be laminated on the PCB board on the operating table of the laminating machine;
[0020] S2: Set the fusion frame, and place the fusion frame on the side of the plate set by the stack;
[0021] S3: setting fusion blocks, and arranging the fusion blocks in a grid in the closed area formed by the fusion frame and the side of the plate;
[0022] S4: setting a prepreg, and setting a prepreg on the surface of the fusion block;
[0023] S5: Lay copper foil, and lay a whole piece of copper foil on the surface of the board, fusion frame, and prepreg;
[0024] S6: performing a pressing process;
[0025] S7: Cutting the board. After the pressing is completed, cut the edge of the board, cut off the fusion frame and the fusion block and prepreg in the fusion frame, and compl...
PUM
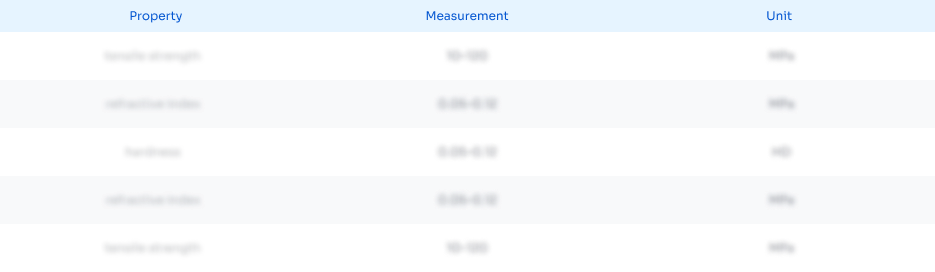
Abstract
Description
Claims
Application Information

- Generate Ideas
- Intellectual Property
- Life Sciences
- Materials
- Tech Scout
- Unparalleled Data Quality
- Higher Quality Content
- 60% Fewer Hallucinations
Browse by: Latest US Patents, China's latest patents, Technical Efficacy Thesaurus, Application Domain, Technology Topic, Popular Technical Reports.
© 2025 PatSnap. All rights reserved.Legal|Privacy policy|Modern Slavery Act Transparency Statement|Sitemap|About US| Contact US: help@patsnap.com