Polyvinyl chloride composite material and preparation process thereof
A polyvinyl chloride and composite material technology, applied in the field of cable materials, can solve the problems of not being able to adapt to the use environment, the material is complex and changeable, and cannot be well protected for use, etc., and achieves good weather resistance and environmental adaptability. Improved scratch resistance, abrasion resistance, and high inertia
- Summary
- Abstract
- Description
- Claims
- Application Information
AI Technical Summary
Problems solved by technology
Method used
Image
Examples
Embodiment 1
[0034] Ingredients: The raw materials are weighed according to the composition and parts by weight of the above polyvinyl chloride composite material, including 100 parts of polyvinyl chloride, 5 parts of nitrile rubber, 13 parts of TOTM plasticizer, 47 parts of KW27 polyester, and 4 parts of soybean oil , 0.2 parts of calcium stearate, 0.8 parts of polyethylene wax, 15 parts of octabromoether, 3 parts of antimony trioxide, 4 parts of CZ-200 rubber vulcanization accelerator, 15 parts of kaolin, 4 parts of calcium carbonate, 2 parts of carbon black , 0.5 parts of titanium dioxide, 1.5 parts of methyl methacrylate, and 4 parts of tetrafluoroethylene copolymer.
[0035] Machine refining: first put polyvinyl chloride, TOTM plasticizer, KW27 polyester, soybean oil, kaolin, calcium carbonate, and methyl methacrylate into the internal mixer, set the processing temperature to 150°C, and process for 15 minutes to obtain the mixture 1 for use, then put the remaining materials into the i...
Embodiment 2-3
[0038] The only difference with Example 1 is that the parts of polyvinyl chloride in the batching of Examples 2-3 are respectively 80 parts and 120 parts.
Embodiment 4
[0040] The only difference with Example 1 is that the parts of TOTM plasticizer in the batching of Example 4 are 10 parts and 40 parts of KW27 polyester.
PUM
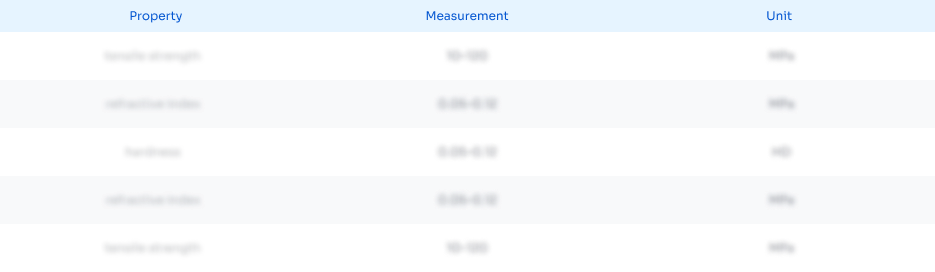
Abstract
Description
Claims
Application Information

- R&D
- Intellectual Property
- Life Sciences
- Materials
- Tech Scout
- Unparalleled Data Quality
- Higher Quality Content
- 60% Fewer Hallucinations
Browse by: Latest US Patents, China's latest patents, Technical Efficacy Thesaurus, Application Domain, Technology Topic, Popular Technical Reports.
© 2025 PatSnap. All rights reserved.Legal|Privacy policy|Modern Slavery Act Transparency Statement|Sitemap|About US| Contact US: help@patsnap.com