Treatment method for enhancing durability of clutch friction plate
A processing method and friction plate technology, applied in the field of auto parts, can solve the problems of slippage, ablation and plastic deformation, surface fracture of the friction plate, etc., and achieve the effects of not easy to scratch, large heat capacity, and enhanced durability
- Summary
- Abstract
- Description
- Claims
- Application Information
AI Technical Summary
Problems solved by technology
Method used
Examples
Embodiment 1
[0015] In the embodiment of the present invention, a treatment method for enhancing the durability of clutch friction plates, the specific method is as follows:
[0016] (1) Submerge the clutch friction plate in an aqueous solution of 8.8% copper acetate for 28 minutes, heat and soak it for 28 minutes, pass it through ultrasonic waves for ultrasonic treatment, take out the drained liquid, put it into steam treatment at a temperature of 77°C for 440 seconds, and heat at 3.3°C / min Raise the temperature to 104°C and continue the steam treatment for 500s, take it out, and get the pretreated clutch friction plate;
[0017] (2) Dry the pretreated clutch friction plate for 10 minutes in a microwave, immerse in the coating solution for 8 minutes, take it out, dry it in a second microwave for 18 minutes, take it out, and vacuum it for 55 minutes at a vacuum degree of 140 MPa;
[0018] The coating liquid is made of the following raw materials in parts by weight: 11 parts of carboxymethy...
Embodiment 2
[0023] In the embodiment of the present invention, a treatment method for enhancing the durability of clutch friction plates, the specific method is as follows:
[0024] (1) Submerge the clutch friction plate in a 9% copper acetate aqueous solution for 30 minutes, heat and soak it for 30 minutes, pass it through an ultrasonic wave for ultrasonic treatment, take out the drained liquid, put it into a steam treatment at a temperature of 79°C for 450s, and heat it at a temperature of 3.5°C / min. Heat up to 106°C and continue steaming for 510s, take it out, and get the pretreated clutch friction plate;
[0025] (2) Dry the pretreated clutch friction plate for 11 minutes in a microwave, immerse in the coating solution for 9 minutes, take it out, dry it in a second microwave for 19 minutes, take it out, and vacuum it for 58 minutes at a vacuum degree of 150 MPa;
[0026] The coating liquid is made of the following raw materials in parts by weight: 11.5 parts of carboxymethyl cellulose...
Embodiment 3
[0031] In the embodiment of the present invention, a treatment method for enhancing the durability of clutch friction plates, the specific method is as follows:
[0032] (1) Submerge the clutch friction plate in an aqueous solution of 9.2% copper acetate for 32 minutes, heat and soak it for 32 minutes, pass it through ultrasonic waves for ultrasonic treatment, take out the drained liquid, put it into steam treatment at a temperature of 81°C for 460 seconds, and heat at 3.7°C / min Heat up to 108°C and continue steaming for 520s, take it out, and get the pretreated clutch friction plate;
[0033] (2) Dry the pretreated clutch friction plate for 12 minutes in a microwave, immerse in the coating solution for 10 minutes, take it out, dry it in a second microwave for 20 minutes, take it out, and vacuum it for 60 minutes at a vacuum degree of 160 MPa;
[0034] The coating liquid is made of the following raw materials in parts by weight: 12 parts of carboxymethyl cellulose, 9 parts of ...
PUM
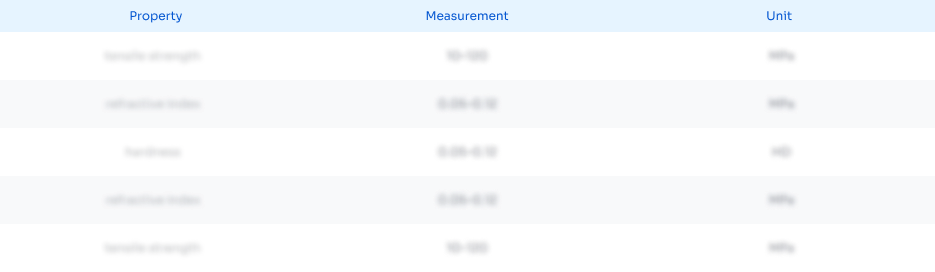
Abstract
Description
Claims
Application Information

- R&D Engineer
- R&D Manager
- IP Professional
- Industry Leading Data Capabilities
- Powerful AI technology
- Patent DNA Extraction
Browse by: Latest US Patents, China's latest patents, Technical Efficacy Thesaurus, Application Domain, Technology Topic, Popular Technical Reports.
© 2024 PatSnap. All rights reserved.Legal|Privacy policy|Modern Slavery Act Transparency Statement|Sitemap|About US| Contact US: help@patsnap.com