Chemical vapor deposition furnace
A chemical vapor deposition and deposition chamber technology, applied in gaseous chemical plating, metal material coating process, coating, etc., can solve problems affecting system pressure, entry, and production, and achieve high product conversion rate and thickness deviation Small, well-structured effects
- Summary
- Abstract
- Description
- Claims
- Application Information
AI Technical Summary
Problems solved by technology
Method used
Image
Examples
Embodiment 1
[0020] see figure 1 , the chemical vapor deposition furnace 100 of the present invention comprises a crucible 110 assembled from bottom to top for containing raw materials, a crucible cover 111 used in conjunction with the crucible 110, a deposition chamber 120, a material receiving box 130, a guide Gas pipe 140; the crucible cover 111 is provided with some first through holes 111a connecting the crucible 110 and the deposition chamber 120, and the receiving box 130 is provided with a second through hole 130a connecting the deposition chamber 120 and the receiving box 130, chemical vapor phase The deposition furnace 100 also includes a first heater 160 for heating the crucible 110, a dust collection chamber 150 and a dust collection chamber cover 151 built in the material receiving box 130 above the dust collection chamber 150, the dust collection chamber cover 151 defines a third through hole 151a that communicates with the dust collection chamber 150 and the material receivi...
Embodiment 2
[0035] see figure 2Most of the structures of Embodiment 2 are the same as those of Embodiment 1, except that the second air inlet pipe 113 ventilates from the water-cooled jacket 190 to the deposition chamber 120, and the second air inlet pipe 113 is vertically inserted into the deposition chamber 120. The two inlet holes 115 are evenly and equidistantly distributed on both sides of the second inlet pipe 113. This design is more conducive to the hydrogen sulfide entering the deposition chamber 120 through the second inlet pipe 113 and the hydrogen sulfide entering the deposition chamber 120 through the first through hole 111a. The zinc vapor is fully mixed to make the chemical reaction more fully.
[0036] It is worth noting that the chemical vapor deposition furnace 100 can also be used to prepare other similar crystals or powders, such as zinc selenide, in addition to being used for preparing zinc sulfide crystals.
[0037] The chemical vapor deposition furnace 100 of the ...
PUM
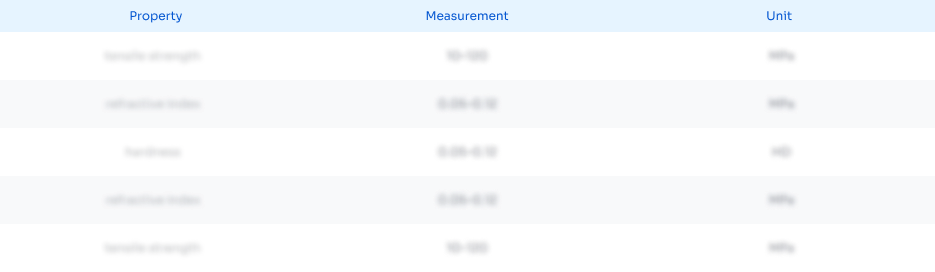
Abstract
Description
Claims
Application Information

- R&D Engineer
- R&D Manager
- IP Professional
- Industry Leading Data Capabilities
- Powerful AI technology
- Patent DNA Extraction
Browse by: Latest US Patents, China's latest patents, Technical Efficacy Thesaurus, Application Domain, Technology Topic, Popular Technical Reports.
© 2024 PatSnap. All rights reserved.Legal|Privacy policy|Modern Slavery Act Transparency Statement|Sitemap|About US| Contact US: help@patsnap.com