Manufacturing method of wooden mold core box
A manufacturing method and technology of wooden molds, applied in the field of mold manufacturing, can solve the problems of short service life of wooden mold core boxes, reduce the probability of deformation, cracking or corrosion, reduce costs, and prevent corrosion
- Summary
- Abstract
- Description
- Claims
- Application Information
AI Technical Summary
Problems solved by technology
Method used
Examples
Embodiment 1
[0018] The manufacture method of the wooden mold core box of the present embodiment may further comprise the steps:
[0019] A. Raw material processing: make wood into several wood laminates of specified size, then clean the wood laminates and put them into a microwave drying kiln for low-temperature drying and sterilization, and then soak the wood laminates in a bonding agent with a concentration of 20%. solution, the soaking time is 10 minutes, and then put the wood laminate into a microwave drying kiln for drying. After drying, the moisture content of the wood laminate is not higher than 10%;
[0020] B. Antiseptic treatment: soak the wood laminate obtained in step A in a 25% preservative solution for 20 minutes, and then put the wood laminate into a microwave drying kiln for drying. After drying, the wood layer The moisture content of the board is not higher than 10%;
[0021] C. Splicing and forming: Prefabricate the casting channel with the wood laminates obtained in st...
Embodiment 2
[0024] The manufacture method of the wooden mold core box of the present embodiment may further comprise the steps:
[0025] A. Raw material processing: make the wood into multiple wood laminates of specified size, then clean the wood laminates and put them into a microwave drying kiln for low-temperature drying and sterilization, and then soak the wood laminates in a bonding agent with a concentration of 22%. solution, the soaking time is 12 minutes, and then put the wood laminate into a microwave drying kiln for drying. After drying, the moisture content of the wood laminate is not higher than 10%;
[0026] B. Anti-corrosion treatment: soak the wood laminate obtained in step A in a 30% preservative solution for 22 minutes, then put the wood laminate into a microwave drying kiln for drying. After drying, the wood layer The moisture content of the board is not higher than 10%;
[0027] C. Splicing and forming: Prefabricate the casting channel with the wood laminates obtained ...
Embodiment 3
[0030] The manufacture method of the wooden mold core box of the present embodiment may further comprise the steps:
[0031] A. Raw material processing: make the wood into multiple wood laminates of specified size, then clean the wood laminates and put them into a microwave drying kiln for low-temperature drying and sterilization, and then soak the wood laminates in a bonding agent with a concentration of 25%. solution, the soaking time is 15 minutes, and then put the wood laminate into a microwave drying kiln for drying. After drying, the moisture content of the wood laminate is not higher than 10%;
[0032] B. Anti-corrosion treatment: soak the wood laminate obtained in step A in a 35% preservative solution for 25 minutes, then put the wood laminate into a microwave drying kiln for drying. After drying, the wood layer The moisture content of the board is not higher than 10%;
[0033] C. Splicing and forming: Prefabricate the casting channel with the wood laminates obtained ...
PUM
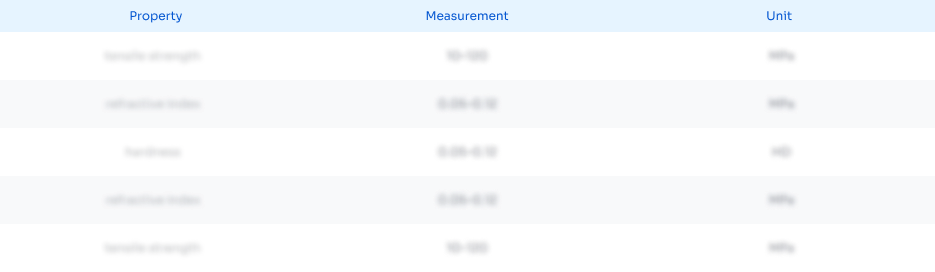
Abstract
Description
Claims
Application Information

- Generate Ideas
- Intellectual Property
- Life Sciences
- Materials
- Tech Scout
- Unparalleled Data Quality
- Higher Quality Content
- 60% Fewer Hallucinations
Browse by: Latest US Patents, China's latest patents, Technical Efficacy Thesaurus, Application Domain, Technology Topic, Popular Technical Reports.
© 2025 PatSnap. All rights reserved.Legal|Privacy policy|Modern Slavery Act Transparency Statement|Sitemap|About US| Contact US: help@patsnap.com