Device and method for preparing super-amphiphobic self-cleaning oil-water separation material
A technology for oil-water separation and preparation equipment, which is applied in the direction of separation methods, liquid separation, chemical instruments and methods, etc., which can solve the problems of pollutant pollution, loss of separation ability, and limitation of the application of oil-water separation membranes, and achieve continuous oil-water separation and recovery of oil-water The effect of separation ability
- Summary
- Abstract
- Description
- Claims
- Application Information
AI Technical Summary
Problems solved by technology
Method used
Image
Examples
Embodiment 1
[0031] Step 1, be that pore density is 100PPI, the foam copper that size is 4.5cm * 3cm * 0.15cm is placed in 100ml copper chloride solution (13.4g copper chloride is added to the hydrochloric acid (30%) of 12.5ml and deionized water prepared in a mixed solution) for etching, and after 7 minutes, take it out. The material after taking out was ultrasonically removed in 1mol / L hydrochloric acid for 10 minutes to remove residual copper chloride, then put into deionized water and absolute ethanol successively for cleaning, and dry at room temperature.
[0032] Step 2: Add 1.72ml of titanium trichloride solution (15%) to 70ml of supersaturated sodium chloride solution to obtain a 0.3mol / L titanium trichloride solution, and stir for 20 minutes. Add 0.14 g of urea to the mixture, and stir for 20 minutes. Take 35ml of the mixed solution and transfer it into a 50ml polytetrafluoroethylene reaction kettle and put it into an oven at 170°C for 4 hours, then cool naturally at room tempera...
Embodiment 2
[0043] Step 1, the pore density is 130PPI, the foamed copper that size is 4.5cm * 3cm * 0.3cm is placed in 100ml cupric chloride solution (6.7g cupric chloride is added to the hydrochloric acid (30%) of 6.25ml and deionized water prepared in the mixed solution) for etching, after 7 minutes, take it out. Ultrasonic in the hydrochloric acid of the material 1mol / L after taking out removes residual cupric chloride for 10 minutes, then put into deionized water and dehydrated alcohol successively to clean, and dry at room temperature.
[0044] Step 2: Add 0.86ml of titanium trichloride solution (15%) to 70ml of supersaturated sodium chloride solution to obtain 0.15mol / L titanium trichloride solution, and stir for 20 minutes. Finally, add 0g of urea into the mixture, stir for 30 minutes, take 35ml of the mixture and transfer it into a 50ml polytetrafluoroethylene reactor and put it in an oven at 180°C for 6 hours, then take it out to cool at room temperature. Finally, the material w...
Embodiment 3
[0049] Step 1, be that pore density is 150PPI, the foam copper that size is 4.5cm * 3cm * 0.1cm is placed in 100ml copper chloride solution (13.4g copper chloride is added to the hydrochloric acid (30%) of 12.5ml and deionized water prepared in a mixed solution) for etching, and after 7 minutes, take it out. Ultrasonic 10 minutes in the hydrochloric acid of the material 1mol / L after taking out removes residual cupric chloride, puts into deionized water and absolute ethanol successively after cleaning, and dries at room temperature.
[0050] Step 2: Add 2.87ml of titanium trichloride solution (15%) to 70ml of supersaturated sodium chloride solution to obtain a 0.5mol / L titanium trichloride solution, and stir for 25 minutes. Finally, add 0.2g of urea into the mixture, stir for 30 minutes, take 35ml of the mixture and transfer it into a 50ml polytetrafluoroethylene reactor and put it in an oven at 190°C for 5 hours, then take it out to cool at room temperature. Finally, the mate...
PUM
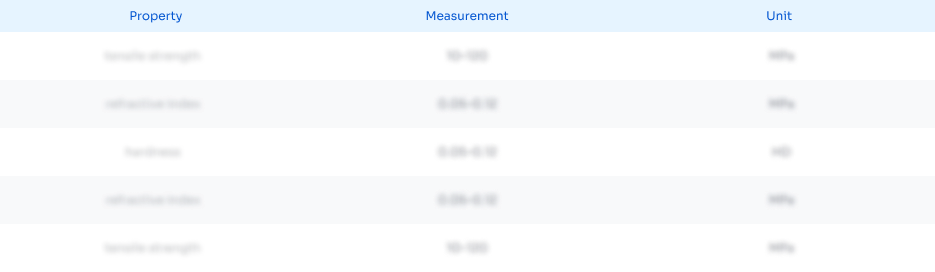
Abstract
Description
Claims
Application Information

- R&D
- Intellectual Property
- Life Sciences
- Materials
- Tech Scout
- Unparalleled Data Quality
- Higher Quality Content
- 60% Fewer Hallucinations
Browse by: Latest US Patents, China's latest patents, Technical Efficacy Thesaurus, Application Domain, Technology Topic, Popular Technical Reports.
© 2025 PatSnap. All rights reserved.Legal|Privacy policy|Modern Slavery Act Transparency Statement|Sitemap|About US| Contact US: help@patsnap.com