Method for preparing high-purity chromate by using ferrochromium
A technology of pure chromate and chromate, applied in the direction of cells, electrolysis process, electrolysis components, etc., to achieve the effect of simplifying process equipment
- Summary
- Abstract
- Description
- Claims
- Application Information
AI Technical Summary
Problems solved by technology
Method used
Image
Examples
preparation example Construction
[0085] Preparation of high-concentration sodium chromate solution: insert a titanium mesh with an outer diameter of 280 mm and an inner diameter of 80 mm, and a stainless steel mesh with an outer diameter of 70 mm in a stainless steel hollow cylinder with an inner diameter of 300 mm. Hollow plastic partitions are used to insulate the titanium mesh and stainless steel. An electrolysis device with double anode and double cathode is formed. Fill the titanium mesh with 100 kg of ferrochrome with a particle size of <100 mm, and fill the electrolytic cell with 44 L of sodium hydroxide solution with a concentration of 260 g / L. The titanium mesh of the electrolytic cell is electrically connected with the positive pole of the power supply, and the stainless steel is electrically connected with the negative pole of the power supply. Turn on the power supply, adjust the output current to 100A, and the cell voltage <2.42V. After 610 hours of continuous electrolytic reaction, the temperat...
Embodiment 1
[0088] Take 500mL of high-concentration sodium chromate solution with a sodium chromate concentration of 530g / L and a carbon content of 5g / L and pass it into the hydrothermal reaction kettle, set the reaction temperature at 280°C, the reaction time for 12h, and the reaction pressure at 8MPa. After the reaction, a solid-liquid mixed slurry was obtained, and the slurry was filtered and separated to obtain 29 g of chromium hydroxide in the solid phase and 470 mL of sodium chromate solution in the liquid phase. The liquid phase was evaporated and concentrated to obtain a sodium chromate product with a purity of 99.1%.
Embodiment 2
[0090] Take sodium chromate concentration and be 260g / L, carbon content is that 500mL of the high-concentration sodium chromate solution of 2.5g / L is passed in the hydrothermal reaction kettle. Set the reaction temperature to 220°C, the reaction time to 2h, and the reaction pressure to 3MPa. After the reaction, a solid-liquid mixed slurry was obtained, and the slurry was filtered and separated to obtain 14 g of chromium hydroxide in the solid phase and 480 mL of sodium chromate solution in the liquid phase. The liquid phase was evaporated and concentrated to obtain a sodium chromate product with a purity of 99.2%.
PUM
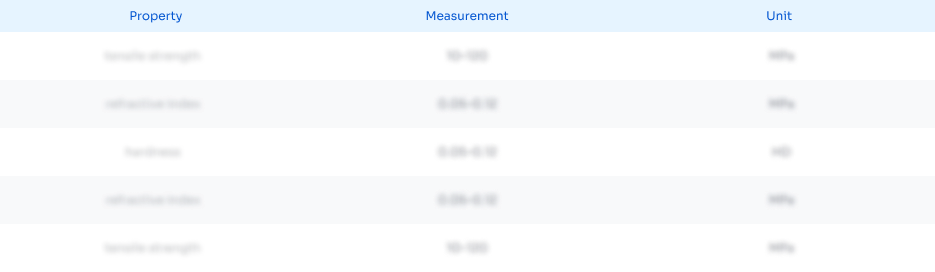
Abstract
Description
Claims
Application Information

- R&D Engineer
- R&D Manager
- IP Professional
- Industry Leading Data Capabilities
- Powerful AI technology
- Patent DNA Extraction
Browse by: Latest US Patents, China's latest patents, Technical Efficacy Thesaurus, Application Domain, Technology Topic, Popular Technical Reports.
© 2024 PatSnap. All rights reserved.Legal|Privacy policy|Modern Slavery Act Transparency Statement|Sitemap|About US| Contact US: help@patsnap.com