Roller method treatment process suitable for total steel slag treatment and treatment device
A processing device and processing technology technology, applied in lighting and heating equipment, furnace components, furnaces, etc., can solve problems such as inability to take into account fluid slag processing, inability to handle, structural limitations, etc.
- Summary
- Abstract
- Description
- Claims
- Application Information
AI Technical Summary
Problems solved by technology
Method used
Image
Examples
Embodiment 1
[0079] A 150-ton electric furnace in a steel factory discharges about 20 tons of slag in each furnace. The slag has good fluidity and uses 18m 3 The slag tank is connected to the slag at the back of the furnace, and then transported 3km to the slag treatment room by a slag tank truck for slag treatment by the roller method. When the slag tank 2 arrives at the slag treatment room, the slag tank 2 is hoisted to the tipping mechanism 1 by the crane. After the slag tank 2 has been accepted by the tipping mechanism, the holding mechanism firmly fixes the slag tank 2 on the tilting platform. And move back and forth to the appropriate position to prepare for the operation of tipping the slag tank into the slag.
[0080]Start the slag conveying and storage system 7 in sequence (i.e. iron remover 77-vibrating screen 76-bucket elevator 78-vibrating screen 73-combined conveyor 71)-drum device 5 (motor 510-1 through coupling 510- 2. Reducer 510-3 and cardan shaft 510-4 and pinion shaft 5...
Embodiment 2
[0087] In the 300-ton converter steelmaking process of a steel plant, slag splashing is used to protect the furnace after tapping to prolong the life of the furnace lining. The slag discharge temperature is low, and the fluidity is poor, or even has no fluidity. About 30 tons of slag is discharged per furnace, and the slag is 33m 3 The slag tank is received and stored, and the rail car is transported. In order to utilize the drum process to process such steel slag, the process is equipped with a remote-operated slag remover 4 .
[0088] When the slag tank 2 arrives at the slag treatment room, the slag tank 2 is hoisted to the tipping mechanism 1 by the crane. After the slag tank 2 has been accepted by the tipping mechanism, the holding mechanism firmly fixes the slag tank 2 on the tilting platform. And move back and forth to the appropriate position to prepare for the operation of tipping the slag tank into the slag.
[0089] Start the slag conveying and storage system 7 in ...
PUM
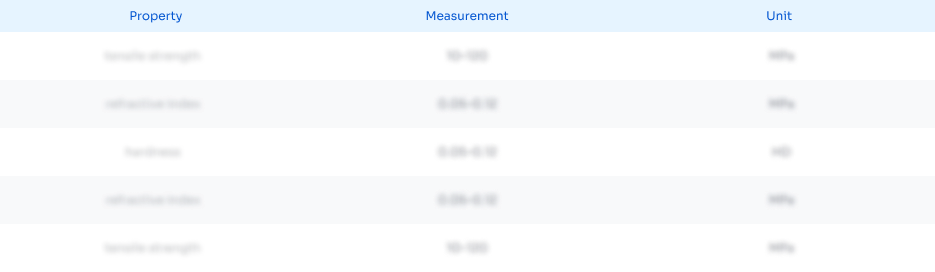
Abstract
Description
Claims
Application Information

- Generate Ideas
- Intellectual Property
- Life Sciences
- Materials
- Tech Scout
- Unparalleled Data Quality
- Higher Quality Content
- 60% Fewer Hallucinations
Browse by: Latest US Patents, China's latest patents, Technical Efficacy Thesaurus, Application Domain, Technology Topic, Popular Technical Reports.
© 2025 PatSnap. All rights reserved.Legal|Privacy policy|Modern Slavery Act Transparency Statement|Sitemap|About US| Contact US: help@patsnap.com