Light-emitting diode and method of making the same
A technology of light-emitting diodes and manufacturing methods, which is applied in the direction of semiconductor devices, electrical components, circuits, etc., can solve the problems of sacrificing the area of the active area, increasing the cost of chip manufacturing, and current congestion, so as to improve the current blocking ability and improve the ohm Effect of contact ability and uniform distribution of current
- Summary
- Abstract
- Description
- Claims
- Application Information
AI Technical Summary
Problems solved by technology
Method used
Image
Examples
Embodiment Construction
[0054] The following will clearly and completely describe the technical solutions in the embodiments of the present invention with reference to the accompanying drawings in the embodiments of the present invention. Obviously, the described embodiments are only some, not all, embodiments of the present invention. Based on the embodiments of the present invention, all other embodiments obtained by persons of ordinary skill in the art without making creative efforts belong to the protection scope of the present invention.
[0055] An embodiment of the present invention provides a light emitting diode, the structure of which is shown in figure 1 As shown, the light-emitting diode includes the following structure:
[0056] A substrate 1, and a buffer layer 2, an unintentionally doped layer 3, a first doped layer 4, a first heavily doped layer 5, a first ohmic contact layer 6, a first Highly doped layer 7, first isolation layer 8, second doped layer 9, first current blocking layer ...
PUM
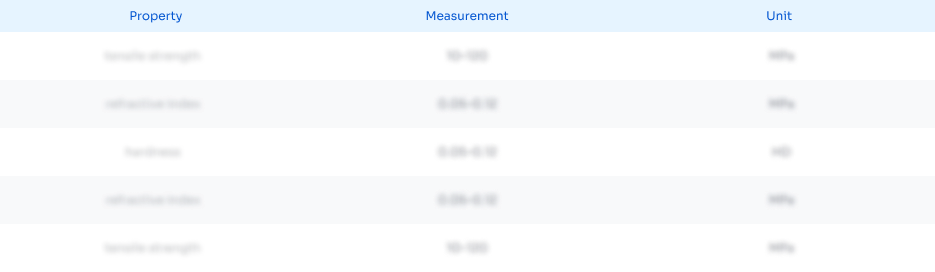
Abstract
Description
Claims
Application Information

- R&D
- Intellectual Property
- Life Sciences
- Materials
- Tech Scout
- Unparalleled Data Quality
- Higher Quality Content
- 60% Fewer Hallucinations
Browse by: Latest US Patents, China's latest patents, Technical Efficacy Thesaurus, Application Domain, Technology Topic, Popular Technical Reports.
© 2025 PatSnap. All rights reserved.Legal|Privacy policy|Modern Slavery Act Transparency Statement|Sitemap|About US| Contact US: help@patsnap.com