Strong-acid high-temperature resistant cationic resin catalyst and preparation method thereof
A cationic resin and high-temperature-resistant technology, which is applied in the direction of catalyst activation/preparation, carboxylate preparation, chemical instruments and methods, etc. It can solve the problems of difficult to meet technical needs, limited application range, unbalanced balance between catalytic activity and temperature resistance, etc. problems, achieving both catalytic activity and high temperature resistance, improved electron distribution, and excellent thermal stability
- Summary
- Abstract
- Description
- Claims
- Application Information
AI Technical Summary
Problems solved by technology
Method used
Image
Examples
Embodiment 1
[0018] Embodiment 1——preparation of catalyst C-1
[0019] ①. Suspension polymerization: add the water phase to the stainless steel stirred tank with a condensing reflux device, add the oil phase when the temperature rises to 60°C, continue to heat up to 80°C during stirring, and react for 8 hours, and the stirring speed is 80 rpm;
[0020] Wherein, by weight, the water phase is a mixture of 20 parts of disodium lauryl sulfosuccinate monoester, 20 parts of potassium monododecyl phosphate and 4000 parts of water; the oil phase is a mixture of 500 parts of styrene parts, 1000 parts of divinylbenzene and 30 parts of benzoyl peroxide;
[0021] ②. Stable structure
[0022] Soak the polymerized white balls obtained in step ① in a solvent, stir and soak for 10 hours at a stirring speed of 80 rpm, then raise the temperature to 80°C and keep it constant for 5 hours, wherein the solvents are n-hexane, n-octane and one of cyclohexane;
[0023] ③.Halogenation
[0024] Soak the resin wh...
Embodiment 2
[0030] Embodiment 2——preparation of catalyst C-2
[0031] ①. Suspension polymerization: Add the water phase to the stainless steel stirred tank with condensing reflux device, add the oil phase when the temperature rises to 70°C, continue to heat up to 90°C during stirring, and react for 10 hours, and the stirring speed is 100 rpm;
[0032] Wherein, by weight, the water phase is a mixture of 50 parts of disodium lauryl sulfosuccinate monoester, 30 parts of potassium monododecyl phosphate and 4200 parts of water; the oil phase is a mixture of 800 parts of styrene 700 parts of divinylbenzene and 30 parts of benzoyl peroxide;
[0033] ②. Stable structure
[0034] Soak the polymerized white balls obtained in step ① in a solvent, stir and soak for 11 hours, the stirring speed is 110 rpm, then raise the temperature to 90°C, and keep it constant for 6 hours, wherein the solvent is n-hexane, n-octane and one of cyclohexane;
[0035] ③. Halogenation
[0036] Immerse the resin white ...
Embodiment 3
[0042] Embodiment 3——preparation of catalyst C-3
[0043] ①. Suspension polymerization: Add the water phase to the stainless steel stirred tank with a condensing reflux device, add the oil phase when the temperature rises to 65°C, continue to heat up to 80°C during stirring, and react for 9 hours, and the stirring speed is 120 rpm;
[0044] Wherein, by weight, the water phase is a mixture of 50 parts of disodium lauryl sulfosuccinate monoester, 40 parts of potassium monododecyl phosphate and 4500 parts of water; the oil phase is 500 parts of styrene parts, 1000 parts of divinylbenzene and 30 parts of benzoyl peroxide;
[0045] ②. Stable structure
[0046] Soak the polymerized white balls obtained in step ① in a solvent, stir and soak for 10 hours at a stirring speed of 100 rpm, then raise the temperature to 90°C and keep it constant for 6 hours, wherein the solvents are n-hexane, n-octane and one of cyclohexane;
[0047] ③.Halogenation
[0048] Immerse the resin white ball...
PUM
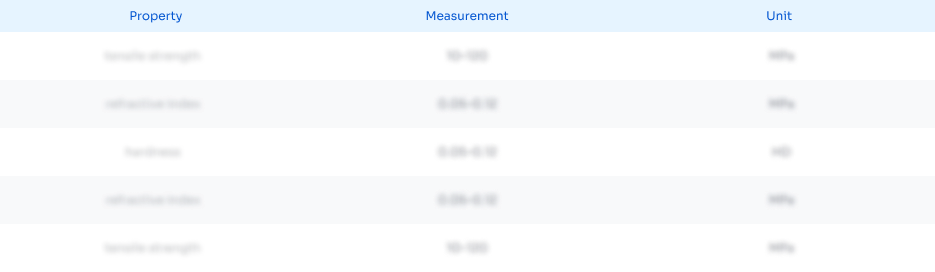
Abstract
Description
Claims
Application Information

- R&D Engineer
- R&D Manager
- IP Professional
- Industry Leading Data Capabilities
- Powerful AI technology
- Patent DNA Extraction
Browse by: Latest US Patents, China's latest patents, Technical Efficacy Thesaurus, Application Domain, Technology Topic, Popular Technical Reports.
© 2024 PatSnap. All rights reserved.Legal|Privacy policy|Modern Slavery Act Transparency Statement|Sitemap|About US| Contact US: help@patsnap.com