Preparation method of composite modified graphite cathode material, composite modified graphite cathode material and application
A graphite negative electrode and composite modification technology, applied in battery electrodes, electrical components, electrochemical generators, etc., can solve the problems of poor rate performance and cycle efficiency of graphite negative electrode materials, and reduce the irreversible capacity of graphite negative electrode materials. Effects of reducing irreversible capacity, increasing reversible capacity, and reducing effective area
- Summary
- Abstract
- Description
- Claims
- Application Information
AI Technical Summary
Problems solved by technology
Method used
Image
Examples
preparation example Construction
[0044] In order to improve the above problems, according to one aspect of the present invention, a method for preparing a composite modified graphite negative electrode material is provided, comprising the following steps:
[0045] mixing the graphite intercalation compound and the phenolic resin mixed solution, drying, and sintering to obtain a composite modified graphite negative electrode material;
[0046] Wherein, the phenolic resin mixed solution mainly includes phenolic resin, phosphorus compound and water.
[0047]The invention provides a preparation method of a composite modified graphite negative electrode material, mainly using a phenolic resin mixed solution to coat and modify a graphite intercalation compound, wherein the graphite intercalation compound is mixed with graphite, an oxidant, and an intercalation agent The oxidation intercalation reaction is carried out, and the phenolic resin mixed solution is mainly composed of phenolic resin, phosphorus compound an...
Embodiment approach
[0082] As a preferred embodiment of the present invention, the preparation method of composite modified graphite negative electrode material comprises the following steps:
[0083] (a) graphite is mixed with oxidant and intercalation agent to carry out oxidative intercalation reaction, and dried to obtain graphite intercalation compound;
[0084] (b) mix and stir the mixed solution of graphite intercalation compound and phenolic resin according to the mass ratio of 1:(7-12) for 1-3h, spray dry, and sinter at 400-800°C for 1-5h to obtain a composite modified graphite negative electrode material ;
[0085] Wherein, the phenolic resin mixed solution mainly includes phenolic resin, phosphoric acid and water, and the mass ratio of phenolic resin, phosphoric acid and water is 1:(4-6):(7-11).
[0086] By limiting the specific process parameters in the preparation method, the coating of the phosphorus-doped carbon coating on the graphite surface is more complete, uniform and firm, re...
Embodiment 1
[0104] A preparation method of composite modified graphite negative electrode material, comprising the following steps:
[0105] (a) Add graphite to the mixed solution of oxidant and intercalant, add the above mixed solution into a water bath, control the temperature of the water bath to about 30°C, stir for 2 hours, and dry at a temperature of 105°C to obtain graphite Intercalation compounds;
[0106] Wherein, the oxidizing agent is formic acid, the intercalating agent is concentrated sulfuric acid, and the mass ratio of graphite, oxidizing agent and intercalating agent is 1:0.2:2.
[0107] (b) The mixed solution of graphite intercalation compound and phenolic resin was mixed and stirred for 2 hours according to the mass ratio of 1:9, spray-dried, sintered at 500°C for 3 hours under a nitrogen atmosphere, and passed through a 200-mesh sieve after grinding to obtain a composite modified graphite negative electrode material ;
[0108] Among them, the phenolic resin mixed solu...
PUM
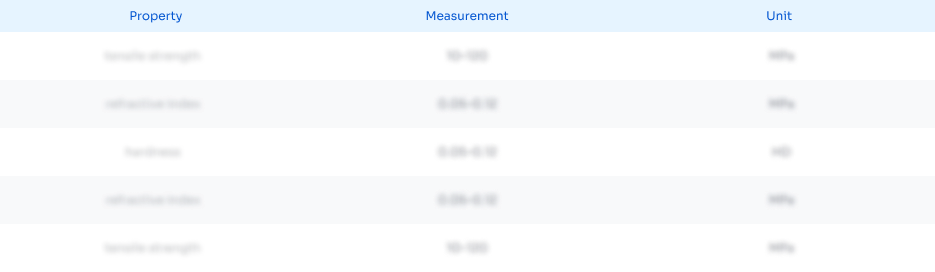
Abstract
Description
Claims
Application Information

- Generate Ideas
- Intellectual Property
- Life Sciences
- Materials
- Tech Scout
- Unparalleled Data Quality
- Higher Quality Content
- 60% Fewer Hallucinations
Browse by: Latest US Patents, China's latest patents, Technical Efficacy Thesaurus, Application Domain, Technology Topic, Popular Technical Reports.
© 2025 PatSnap. All rights reserved.Legal|Privacy policy|Modern Slavery Act Transparency Statement|Sitemap|About US| Contact US: help@patsnap.com