Modified phenolic insulation board with nitrogen as foaming agent
A technology of phenolic insulation board and foaming agent, which is applied in the field of building energy-saving materials, can solve the problems of wasting petroleum resources, reducing fire prevention effect, and high cost, and achieves the effects of reducing production cost, increasing fire safety, and strong surface adsorption
- Summary
- Abstract
- Description
- Claims
- Application Information
AI Technical Summary
Problems solved by technology
Method used
Image
Examples
Embodiment 1
[0019] The modified phenolic insulation board with nitrogen as foaming agent is prepared from the following raw materials in parts by weight: 55 parts of thermosetting phenolic resin; 40 parts of nitrogen; 10 parts of fumed silica; 30 parts of curing agent; foam stabilizer 5 parts; 5 parts of toughening modifier.
[0020] The acid curing agent is a 1:1 mixed solvent of phosphoric acid and ethylene glycol. The foam stabilizer is silicon carbon type silicone oil (DC-193). The toughening modifier is polyhexamethylene adipamide (modified nylon 66).
[0021] Concrete preparation process is as follows:
[0022] 1) Premix thermosetting phenolic resin, fumed silica, silicon carbon type silicone oil (DC-193) and polyhexamethylene adipamide (modified nylon 66) according to the ratio of raw materials to form mixture A ;
[0023] 2) Add the mixture A obtained in step 1 as the foaming raw material and the acid curing agent (1:1 mixed solvent of phosphoric acid and ethylene glycol) to t...
Embodiment 2
[0025] The modified phenolic insulation board with nitrogen as foaming agent is prepared from the following raw materials in parts by weight: 85 parts of thermosetting phenolic resin; 30 parts of nitrogen; 25 parts of fumed silica; 15 parts of curing agent; foam stabilizer 8 parts; toughening modifier 10 parts.
[0026] Concrete preparation process is as follows:
[0027] 1) Premix thermosetting phenolic resin, fumed silica, polyoxyethylene condensate and polyhexamethylene adipamide (modified nylon 66) according to the ratio of raw materials to form mixture A;
[0028] 2) Add the mixture A obtained in step 1 as the foaming raw material and the acid curing agent (1:1 mixed solvent of phosphoric acid and ethylene glycol) to the stirring system according to the weight ratio. During the stirring process, feed nitrogen into the stirring system , adjust the nitrogen pressure in the range of 0.6Mpa-0.8Mpa; the total amount of nitrogen gas introduced is controlled within the aforemen...
Embodiment 3
[0030] The modified phenolic insulation board with nitrogen as foaming agent is prepared from the following raw materials in parts by weight: 60 parts of thermosetting phenolic resin; 25 parts of nitrogen; 5 parts of fumed silica; 20 parts of curing agent; foam stabilizer 8 parts; toughening modifier 8 parts.
[0031] Concrete preparation process is as follows:
[0032] 1) Premix thermosetting phenolic resin, fumed silica, polyoxyethylene condensate and polyhexamethylene adipamide (modified nylon 66) according to the ratio of raw materials to form mixture A;
[0033] 2) Add the mixture A obtained in step 1 as the foaming raw material and the acid curing agent (1:1 mixed solvent of phosphoric acid and ethylene glycol) to the stirring system according to the weight ratio. During the stirring process, feed nitrogen into the stirring system , adjust the nitrogen pressure in the range of 0.6Mpa-0.8Mpa; pass the total amount of nitrogen gas into the aforementioned range of parts by...
PUM
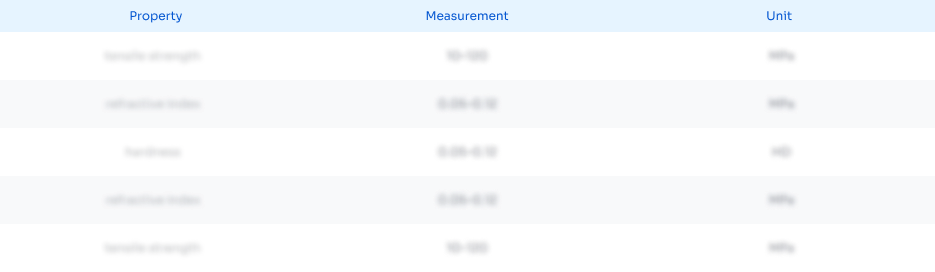
Abstract
Description
Claims
Application Information

- R&D Engineer
- R&D Manager
- IP Professional
- Industry Leading Data Capabilities
- Powerful AI technology
- Patent DNA Extraction
Browse by: Latest US Patents, China's latest patents, Technical Efficacy Thesaurus, Application Domain, Technology Topic, Popular Technical Reports.
© 2024 PatSnap. All rights reserved.Legal|Privacy policy|Modern Slavery Act Transparency Statement|Sitemap|About US| Contact US: help@patsnap.com