Method capable of reducing thickness of decarburized layer of hot-rolled heavy rail steel
A technology of heavy rail steel and decarburization layer, which is applied in the field of steel rolling, can solve the problems of long heating time affecting the decarburization pass rate of decarburization layer thickness, and achieve the effects of avoiding decarburization layer exceeding the standard, strong operability and remarkable effect
- Summary
- Abstract
- Description
- Claims
- Application Information
AI Technical Summary
Problems solved by technology
Method used
Image
Examples
Embodiment 1-8
[0011] Embodiments 1-8: The method for instinctively reducing the thickness of the decarburized layer of hot-rolled heavy rail steel adopts the following specific process.
[0012] (1) The type of the heavy rail steel is U75V-T, and the component content of each example is shown in Table 1.
[0013] Table 1: Component content (wt%) of each example
[0014]
[0015] In Table 1, the balance is Fe and inevitable impurities.
[0016] (2) The process parameters of each embodiment and the thickness of the decarburized layer of the obtained products are shown in Table 2.
[0017] Table 2: Process parameters and thickness of decarburized layer for each example
[0018]
PUM
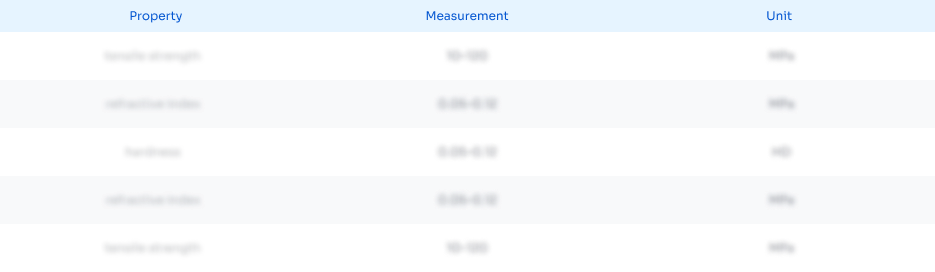
Abstract
Description
Claims
Application Information

- Generate Ideas
- Intellectual Property
- Life Sciences
- Materials
- Tech Scout
- Unparalleled Data Quality
- Higher Quality Content
- 60% Fewer Hallucinations
Browse by: Latest US Patents, China's latest patents, Technical Efficacy Thesaurus, Application Domain, Technology Topic, Popular Technical Reports.
© 2025 PatSnap. All rights reserved.Legal|Privacy policy|Modern Slavery Act Transparency Statement|Sitemap|About US| Contact US: help@patsnap.com