Method for reducing aluminum oxide inclusion in semi-steel steelmaking casting blank
An alumina and casting billet technology, applied in the direction of manufacturing converters, etc., can solve the problems of increased consumption of aluminum and iron, unfavorable performance of molten steel and steel products, and increased production costs, so as to reduce deoxidation costs, reduce Al2O3 inclusions, and improve casting billets. quality effect
- Summary
- Abstract
- Description
- Claims
- Application Information
AI Technical Summary
Problems solved by technology
Method used
Examples
Embodiment 1
[0034] The 140t converter adopts semi-steel steelmaking to smelt Q235 steel grade, and the process path is as follows:
[0035] Molten iron pretreatment → top-bottom combined blowing converter → RH → continuous casting.
[0036] Hot metal: C 3.2-4.1wt%, Si 0.015-0.030wt%, Mn 0.02-0.04wt%, P 0.06-0.08wt%, S≤0.025wt%.
[0037] The KR method is used for desulfurization to pretreat the molten iron, and the sulfur content in the molten iron after pretreatment is ≤0.015%.
[0038] The specific method of top-bottom combined blowing converter is as follows:
[0039] Put molten iron at 1300~1360℃ and start blowing oxygen, the oxygen flow rate is 30000Nm 3 / h. Start adding auxiliary materials after 3 minutes of blowing.
[0040] The oxygen lance nozzle is 1.4-2m away from the metal liquid surface of the molten pool, the blowing lance is 1.4m-1.8m, the blowing lance is 2m, and the carbon pulling lance is 1.4m. The gun position of the oxygen lance refers to the distance from the end ...
Embodiment 2
[0045] According to the method described in Example 1, semi-steel steelmaking is used to smelt Q235 steel; the difference from Example 1 is that the control requirements of the top-bottom combined blowing converter are that the end point carbon content is 0.07%, and the end point temperature is 1670 ° C. The sliding plate slag blocking system is adopted in the tapping process of the converter, and the amount of slag dropped is controlled to 29mm, and the aluminum-iron deoxidation is not used in the tapping process of the converter.
[0046] The treatment requirements of the RH process are that the RH entry temperature is 1610°C, and carbon deoxidation is carried out directly; the RH entry cycle is 4.5min, and the deoxidation alloying is carried out.
Embodiment 3
[0048] According to the method described in Example 1, semi-steel steelmaking is used to smelt Q235 steel; the difference from Example 1 is that RH enters the station and circulates for 4 minutes for deoxidation and alloying.
PUM
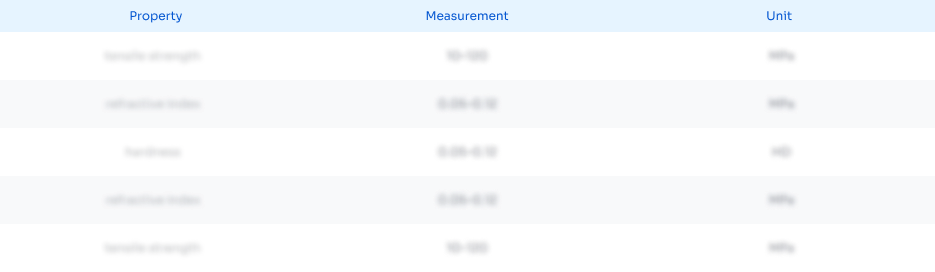
Abstract
Description
Claims
Application Information

- R&D
- Intellectual Property
- Life Sciences
- Materials
- Tech Scout
- Unparalleled Data Quality
- Higher Quality Content
- 60% Fewer Hallucinations
Browse by: Latest US Patents, China's latest patents, Technical Efficacy Thesaurus, Application Domain, Technology Topic, Popular Technical Reports.
© 2025 PatSnap. All rights reserved.Legal|Privacy policy|Modern Slavery Act Transparency Statement|Sitemap|About US| Contact US: help@patsnap.com