Micro-channel integrated cold plate based on a micro-channel porous flat tube and making method thereof
A micro-channel and flat-tube technology, applied in electrical components, electrical solid devices, circuits, etc., can solve the problems of leakage and heat conduction, affecting sealing, poor and other problems, and achieve the effect of matching expansion coefficient and reducing thermal resistance.
- Summary
- Abstract
- Description
- Claims
- Application Information
AI Technical Summary
Problems solved by technology
Method used
Image
Examples
specific Embodiment
[0054] Specific embodiment: Based on the present invention, a liquid-cooled heat dissipation component is processed, and the liquid-cooled micro-channel flat tube is embedded in the bottom plate of the box body to realize rapid prototyping and welding. At the same time, the matching of the thermal expansion coefficient of the chip and the cold plate is taken into account, and the expectation is achieved. cooling effect. Specific implementation examples such as Figure 8 : In this example, the bottom plate of the box body is used as the base plate and structural support of the cold plate at the same time. Mounting ears are arranged on the outside of the box body for external connection of the box body. The outer dimension of the box body is 46mm*31mm*7mm. The inside of the box body is processed with a flow channel cavity and a confluence cavity, and the flow channel cavity is embedded with two porous flat tubes arranged in series. The flat tube is 21mm long and 13mm wide, with...
PUM
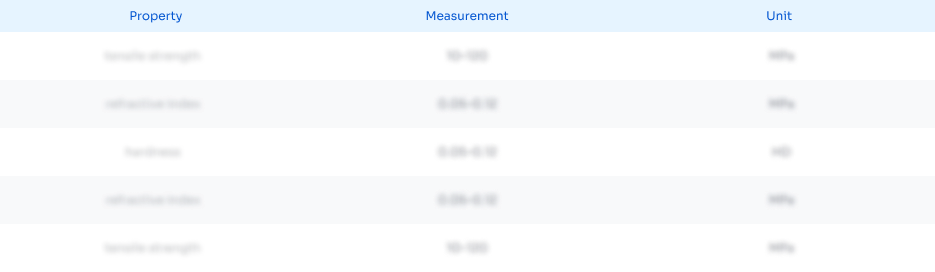
Abstract
Description
Claims
Application Information

- Generate Ideas
- Intellectual Property
- Life Sciences
- Materials
- Tech Scout
- Unparalleled Data Quality
- Higher Quality Content
- 60% Fewer Hallucinations
Browse by: Latest US Patents, China's latest patents, Technical Efficacy Thesaurus, Application Domain, Technology Topic, Popular Technical Reports.
© 2025 PatSnap. All rights reserved.Legal|Privacy policy|Modern Slavery Act Transparency Statement|Sitemap|About US| Contact US: help@patsnap.com