Permanent antistatic micro-foaming polypropylene composite material and preparation method thereof
A permanent antistatic agent and composite material technology, applied in the field of polymer materials, can solve problems such as static electricity accumulation, achieve the effects of eliminating shrinkage marks, shortening injection molding cycle, and reducing weight
- Summary
- Abstract
- Description
- Claims
- Application Information
AI Technical Summary
Problems solved by technology
Method used
Image
Examples
Embodiment 1
[0028] The permanent antistatic micro-foamed polypropylene composite material in the present embodiment is made up of following raw materials by weight:
[0029]
[0030] Concrete preparation method comprises the following steps:
[0031] (1) Weigh the antistatic agent MH1657 and polypropylene resin at a weight ratio of 20:80, extrude and granulate at 190°C through a screw extruder, and dry to obtain an antistatic masterbatch;
[0032] (2) 55 parts of copolymerized polypropylene resin, 8 parts of toughening agent POE8842, 5 parts of talcum powder HTPultra5L, 20 parts of antistatic masterbatch, 0.2 part of antioxidant 1076, 0.2 part of light stabilizer 3808PP5 and 0.5 part of lubricant Add TR451 together to a high-speed mixer and mix for 5 minutes;
[0033] (3) Add the material in step (2) into the twin-screw extruder through the main feeding hopper, and obtain a permanent antistatic polypropylene composite material through melting, extruding, pelletizing, and drying; where...
Embodiment 2
[0036] The permanent antistatic micro-foamed polypropylene composite material in the present embodiment is made up of following raw materials by weight:
[0037]
[0038] Concrete preparation method comprises the following steps:
[0039] (1) Weigh the antistatic agent and polypropylene resin in a weight ratio of 20:80, extrude and granulate at 200°C through a screw extruder, and dry to obtain an antistatic masterbatch;
[0040] (2) 70 parts of copolymerized polypropylene resin, 5 parts of toughening agent POE875L, 5 parts of calcium carbonate JX8000, 15 parts of antistatic masterbatch, 0.3 parts of antioxidant 1076, 0.2 parts of antioxidant 168, 0.4 parts of light stabilizer Add 5585 and 0.6 parts of lubricant TM-2153 into the high-speed mixer and mix for 4 minutes;
[0041] (3) Add the material in step (2) into the twin-screw extruder through the main feeding hopper, and obtain a permanent antistatic polypropylene composite material through melting, extruding, pelletizin...
Embodiment 3
[0044] The low-odor polypropylene composite material in the present embodiment is made up of following raw material by weight:
[0045]
[0046] Concrete preparation method comprises the following steps:
[0047] (1) Weigh the antistatic agent and polypropylene resin in a weight ratio of 20:80, extrude and granulate at 190°C through a screw extruder, and dry to obtain an antistatic masterbatch;
[0048](2) 60 parts of copolymerized polypropylene resin, 5 parts of toughening agent POE875L, 5 parts of calcium carbonate ML838, 5 parts of antistatic masterbatch, 0.3 parts of antioxidant 1076, 0.2 parts of antioxidant 168, 0.2 parts of light stabilizer Add 3853PP5 and 0.6 parts of lubricant TM-2153 into the high-speed mixer and mix for 3 minutes;
[0049] (3) Add the material in step (2) into the twin-screw extruder through the main feeding hopper, and obtain a permanent antistatic polypropylene composite material through melting, extruding, pelletizing, and drying; wherein, th...
PUM
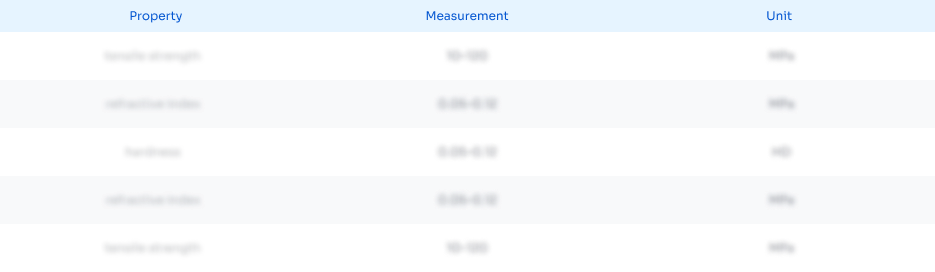
Abstract
Description
Claims
Application Information

- R&D Engineer
- R&D Manager
- IP Professional
- Industry Leading Data Capabilities
- Powerful AI technology
- Patent DNA Extraction
Browse by: Latest US Patents, China's latest patents, Technical Efficacy Thesaurus, Application Domain, Technology Topic, Popular Technical Reports.
© 2024 PatSnap. All rights reserved.Legal|Privacy policy|Modern Slavery Act Transparency Statement|Sitemap|About US| Contact US: help@patsnap.com