Hydraulic press for pressing metal
A hydraulic press and metal technology, applied in the field of hydraulic presses, can solve the problems of large heat dissipation area on the side of the mold, large waste of heat energy, inconvenient operation, etc., and achieve the effect of reducing labor intensity of workers, reducing heat dissipation surface, and simple structure
- Summary
- Abstract
- Description
- Claims
- Application Information
AI Technical Summary
Problems solved by technology
Method used
Image
Examples
Embodiment Construction
[0017] In order to further understand the invention content, characteristics and effects of the present invention, the following examples are given, and detailed descriptions are as follows in conjunction with the accompanying drawings:
[0018] see figure 1 , figure 2 , between the upper beam 3 and the lower beam 7, two columns 4 are connected by nuts 2, the master cylinder 1 and the guide rod 5 are installed on the upper beam, the backing plate 13 is installed at the lower end of the master cylinder and the guide rod, and the backing plate The lower end is vertically equipped with a pressure column 12, and the lead cylinder 6 matched with the pressure column is installed on the lower beam, and the roller 11 of guiding the lead bar is installed on the lead cylinder upper end. The rear of the lower beam is provided with a lead coiler 14 and a feeding mechanism 15, such as image 3 , Figure 4 As shown, the lead coiler has a base 14-18, a left bracket 14-16 and a right brac...
PUM
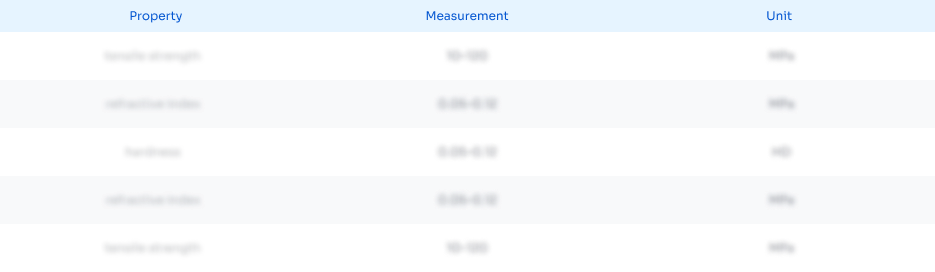
Abstract
Description
Claims
Application Information

- R&D Engineer
- R&D Manager
- IP Professional
- Industry Leading Data Capabilities
- Powerful AI technology
- Patent DNA Extraction
Browse by: Latest US Patents, China's latest patents, Technical Efficacy Thesaurus, Application Domain, Technology Topic, Popular Technical Reports.
© 2024 PatSnap. All rights reserved.Legal|Privacy policy|Modern Slavery Act Transparency Statement|Sitemap|About US| Contact US: help@patsnap.com