A kind of open cavity extrusion molding die
An extrusion forming and open technology, which is applied in the direction of forming tools, manufacturing tools, metal processing equipment, etc., can solve the problems of increasing repeated heating and drawing processes, long manufacturing process, easy to produce coarse grains, etc., to improve the forming performance and quality, reduce the forming process, and prevent the effect of shear deformation
- Summary
- Abstract
- Description
- Claims
- Application Information
AI Technical Summary
Problems solved by technology
Method used
Image
Examples
Embodiment Construction
[0026] Embodiments of the present invention will be described below in conjunction with the accompanying drawings.
[0027] (1) The size of the product forging is as follows: Figure 4 , Inner diameter Ф76mm, outer diameter Ф100mm, inner hole length 540mm, total product length 632mm, blank blanking diameter design Ф120mm.
[0028] (2) Firstly, simulate and analyze the extrusion process of the open cavity as follows: Figure 5 , in the extrusion punching stage of the open cavity, when the initial plastic deformation resistance of the material is reached, the stress increases rapidly, which is related to the deformation characteristics of the material; then the open cavity creates good conditions for deformation, which is conducive to eliminating Due to the influence of work hardening, the forming pressure decreases rapidly; with the gradual reduction of the open cavity, the forming load increases significantly, but the overall stress is not large. In the extrusion and drawing...
PUM
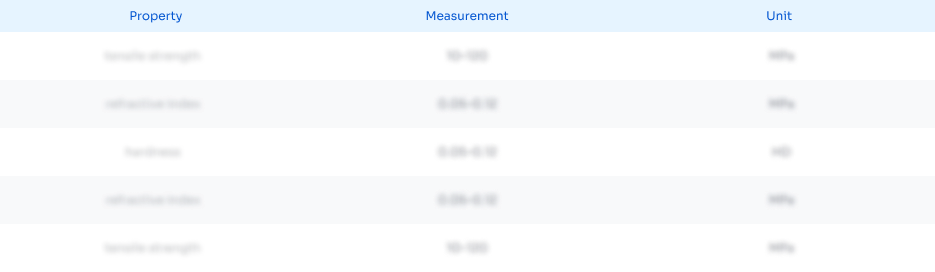
Abstract
Description
Claims
Application Information

- Generate Ideas
- Intellectual Property
- Life Sciences
- Materials
- Tech Scout
- Unparalleled Data Quality
- Higher Quality Content
- 60% Fewer Hallucinations
Browse by: Latest US Patents, China's latest patents, Technical Efficacy Thesaurus, Application Domain, Technology Topic, Popular Technical Reports.
© 2025 PatSnap. All rights reserved.Legal|Privacy policy|Modern Slavery Act Transparency Statement|Sitemap|About US| Contact US: help@patsnap.com