A method of producing a rotor
A production method and rotor technology, which is applied in the manufacture of stator/rotor bodies, electromechanical devices, electrical components, etc., can solve the problem of heavy grinding or insert work, the accuracy cannot be guaranteed, and the heavy workload of assembling and disassembling molds, etc. problems, to achieve the effect of easy processing, enhanced competitiveness, convenient and reliable maintenance
- Summary
- Abstract
- Description
- Claims
- Application Information
AI Technical Summary
Problems solved by technology
Method used
Examples
Embodiment Construction
[0033] The invention provides a rotor production method with the advantages of simple process, convenient operation, convenient and reliable maintenance, high process capability coefficient, high productivity, low cost, and improved competitiveness of enterprise products.
[0034] In order to make the object, technical solution and advantages of the present invention clearer, the present invention will be further described in detail below in conjunction with specific examples.
[0035] In an exemplary embodiment of the present invention, a method for producing a rotor is provided, which includes the following steps: (1) Punching: the blanking and punching of the stator sheet is completed in one step, and the rotor punching is positioned on the inner circle, using a single process punching ;
[0036] (2) Laminated iron core: Automatically stack the rotor punches that have been slotted in step (1) to form a rotor iron core;
[0037] (3) Pressing the rotor main body: Pressing th...
PUM
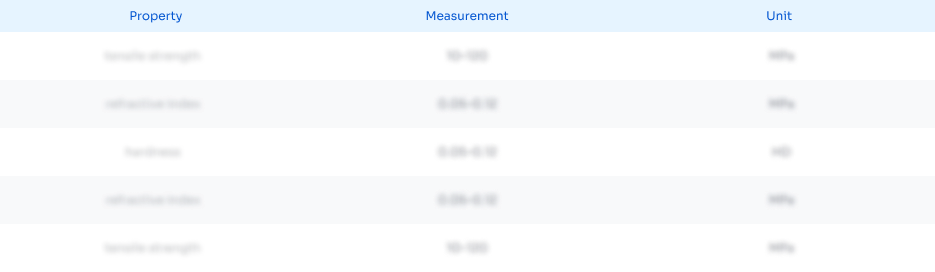
Abstract
Description
Claims
Application Information

- Generate Ideas
- Intellectual Property
- Life Sciences
- Materials
- Tech Scout
- Unparalleled Data Quality
- Higher Quality Content
- 60% Fewer Hallucinations
Browse by: Latest US Patents, China's latest patents, Technical Efficacy Thesaurus, Application Domain, Technology Topic, Popular Technical Reports.
© 2025 PatSnap. All rights reserved.Legal|Privacy policy|Modern Slavery Act Transparency Statement|Sitemap|About US| Contact US: help@patsnap.com