Overall rotary type solid thermal carrier retort
A solid heat carrier, rotary technology, applied in special forms of dry distillation, dry distillation combined with direct and indirect heating, coke oven, etc., can solve the problem of power consumption, large amount of dusty gas treatment, tar and semi-coke particle system pipeline blockage , high thermal efficiency of the system, etc., to achieve the effects of short pyrolysis time, avoiding secondary decomposition, and improving oil recovery
- Summary
- Abstract
- Description
- Claims
- Application Information
AI Technical Summary
Problems solved by technology
Method used
Image
Examples
Embodiment Construction
[0038] The technical solutions of the present invention will be further described below in conjunction with the accompanying drawings and through specific implementation methods.
[0039] The integral rotary solid heat carrier dry distillation furnace described in this embodiment, such as figure 1 As shown, the retort furnace is suitable for the pyrolysis of pulverized coal with a particle size of 10mm or less. The retort furnace is of an integral rotary structure, including a furnace outer cylinder 1. The furnace outer cylinder 1 includes a fixed outer cylinder 101 and a rotary outer cylinder 102. One end of the fixed outer cylinder 101 is provided with a silo 7, the other end of the fixed outer cylinder 101 is connected to the rotary outer cylinder 102 with a first dynamic seal 15, and the fixed outer cylinder 101 is provided with a flue gas outlet 1012 and a semi-coke outlet 1011.
[0040]The rotary outer cylinder 102 includes a preheating chamber 2, a carbonization chambe...
PUM
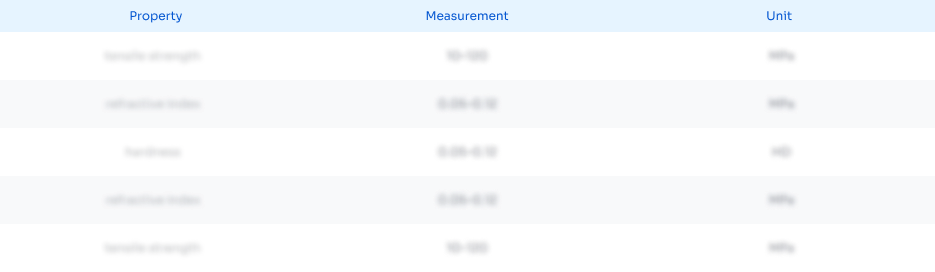
Abstract
Description
Claims
Application Information

- Generate Ideas
- Intellectual Property
- Life Sciences
- Materials
- Tech Scout
- Unparalleled Data Quality
- Higher Quality Content
- 60% Fewer Hallucinations
Browse by: Latest US Patents, China's latest patents, Technical Efficacy Thesaurus, Application Domain, Technology Topic, Popular Technical Reports.
© 2025 PatSnap. All rights reserved.Legal|Privacy policy|Modern Slavery Act Transparency Statement|Sitemap|About US| Contact US: help@patsnap.com