Preparation method of cement foamed heat insulation board
A cement foaming and thermal insulation board technology, applied in the field of building materials, can solve the problems of reduced compressive strength, stress concentration, uneven distribution, etc., and achieve the effects of uniform distribution, prevention of cracking, and uniform pore size.
- Summary
- Abstract
- Description
- Claims
- Application Information
AI Technical Summary
Problems solved by technology
Method used
Examples
preparation example Construction
[0021] The preparation method of cement foam insulation board of the present invention comprises the following steps:
[0022] (1) According to the number of parts by weight, the raw materials are taken, 95-100 parts of cement, 30-40 parts of water, 8-10 parts of composite foaming agent, 6-9 parts of silicon-acrylic emulsion, 3-5 parts of additives, 1 ~2 parts of water reducing agent and 1.4~1.5 parts of catalyst;
[0023] (2) First put cement, silicon acrylic emulsion, water reducer and catalyst into the mixer, stir and mix at 300r / min for 30-50min, then add water, stir at 50-60℃ for 20-30min, then add compound hair After the foaming agent and auxiliary agent continue to stir for 1-2 hours, collect the stirred mixture, put it into a mold, and place the mold at 70-80°C for 3-5 hours to stand still for foaming;
[0024] (3) After the foaming is completed, put the mold at room temperature and let it stand for 3-6 hours, then demould, collect the demoulding material, maintain an...
example 1
[0026] The preparation of cement in the present invention: According to the mass ratio of 3:1, ordinary Portland cement (manufacturer: Shanghai Sixu Engineering Technology Co., Ltd.), sulphoaluminate cement (manufacturer: Hangzhou Yaowei Building Material Technology Co., Ltd.) Put it in a blender and mix well.
[0027] Preparation of composite foaming agent: Mix sodium lauroyl sarcosinate, N-acyl glutamate and 1.6mol / L hydrogen peroxide at a mass ratio of 1:1:5.
[0028] Preparation of additives: Mix polyglutamic acid and sodium dodecylbenzenesulfonate evenly at a mass ratio of 4:1.
[0029] The choice of water reducing agent is amino water reducing agent (manufacturer: Shaanxi Qinfen Building Materials Co., Ltd.).
[0030] Catalyst preparation: mix titanium dioxide and manganese dioxide at a mass ratio of 1:3.
[0031] The preparation method of cement foam insulation board of the present invention comprises the following steps:
[0032] (1) According to parts by weight, th...
example 2
[0036] The preparation of cement in the present invention: According to the mass ratio of 4:1, ordinary Portland cement (manufacturer: Shanghai Sixu Engineering Technology Co., Ltd.), sulphoaluminate cement (manufacturer: Hangzhou Yaowei Building Material Technology Co., Ltd.) Put it in a blender and mix well.
[0037] Preparation of composite foaming agent: Mix sodium lauroyl sarcosinate, N-acyl glutamate and 1.6mol / L hydrogen peroxide at a mass ratio of 1:1:5.
[0038] Preparation of additives: Mix polyglutamic acid and sodium dodecylbenzenesulfonate evenly at a mass ratio of 5:1.
[0039] The choice of water reducing agent is polycarboxylate high-performance water reducing agent (manufacturer: Shaanxi Qinfen Building Materials Co., Ltd.).
[0040] Catalyst preparation: mix titanium dioxide and manganese dioxide at a mass ratio of 1:3.
[0041] The preparation method of cement foam insulation board of the present invention comprises the following steps:
[0042] (1) Accor...
PUM
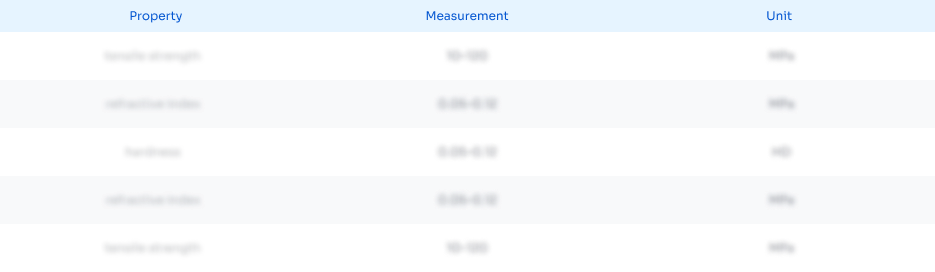
Abstract
Description
Claims
Application Information

- Generate Ideas
- Intellectual Property
- Life Sciences
- Materials
- Tech Scout
- Unparalleled Data Quality
- Higher Quality Content
- 60% Fewer Hallucinations
Browse by: Latest US Patents, China's latest patents, Technical Efficacy Thesaurus, Application Domain, Technology Topic, Popular Technical Reports.
© 2025 PatSnap. All rights reserved.Legal|Privacy policy|Modern Slavery Act Transparency Statement|Sitemap|About US| Contact US: help@patsnap.com